Alumiini on tällä hetkellä yksi yleisimmistä 3D-tulostettavista metallimateriaaleista. Sen käyttö on lisääntynyt erityisesti piensarjatuotannossa alumiinivalujen korvaajana. Taustalla on materiaaliominaisuuksien lisäksi luonnollisesti myös kustannustekijät. Alumiinijauhe on metallijauheista edullisin ja sen valmistusnopeudet ovat suurempia kuin esimerkiksi vaikka teräksellä. Yleisin jauhepetitulostuksessa käytetty alumiiniseos on AlSi10Mg.
Tässä kirjoituksessa kuvataan alumiinin 3D-tulostukseen liittyviä asioita yleisellä tasolla, kun kyseessä on jauhepetimenetelmään perustuva 3D-tulostin. Jauhepetimenetelmä on lisäävän valmistuksen prosessi jossa kappale valmistetaan inertissä valmistuskammiossa sulattamalla jauhepedin alueita selektiivisesti yhteen kerros kerrokselta. Kyseessä on tällä hetkellä yleisin teollisuuden käyttämä metallin 3D-tulostusmenetelmä. Tarkempi kuvaus menetelmän toiminnasta löytyy esimerkiksi Savonian ”Lisäävän valmistuksen Perusteet” –julkaisusta, sivulta 31. (linkki: http://portal.savonia.fi/amk/fi/tutkimus-ja-kehittaminen/julkaisutoiminta/julkaisut-aloittain/tekniikka-ja-liikenne/lisaavan)
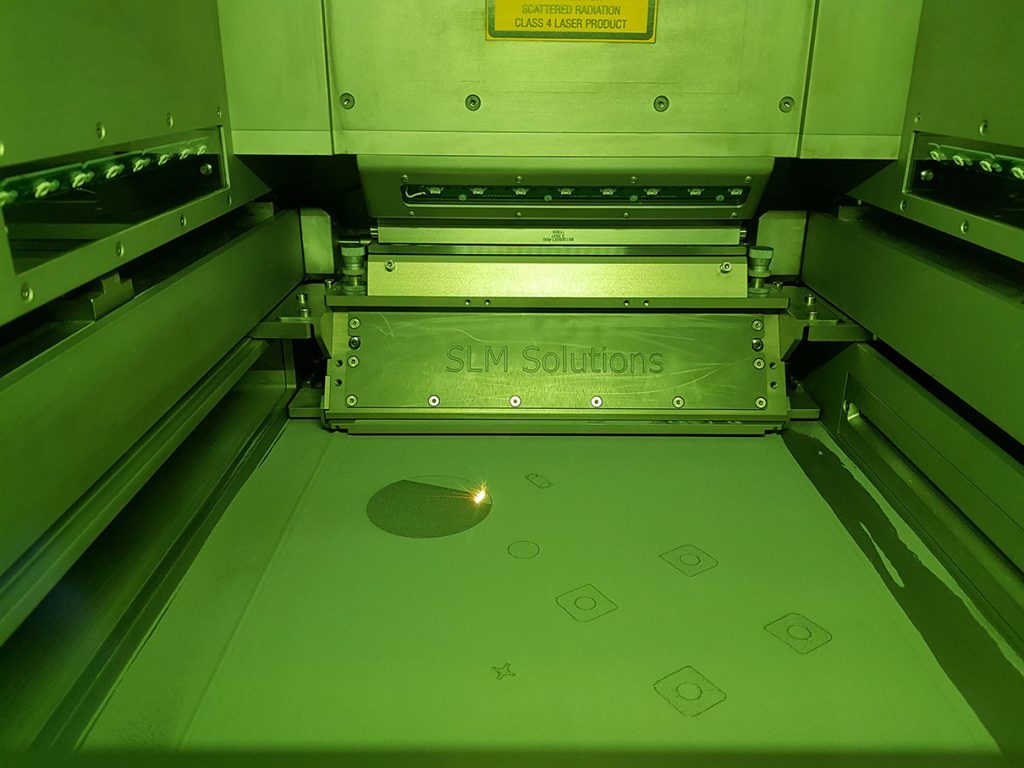
Prosessissa kuvatut työvaiheet ja kuvat ovat peräisin Nivalan Elme Studion 3D-tulostusympäristöstä, jossa Oulun Yliopiston, Kerttu Saalasti -instituutin tulevaisuuden tuotantoteknologiat (FMT) –ryhmän (http://www.oulu.fi/fmt/) asiantuntijat opastivat Savonian 3D-tulostusympäristön henkilökuntaa alumiinin 3D-tulostuksessa. Elme Studiolla on käytössä SLM 280 –metallitulostin ja valmistelevat toimenpiteet tehdään Materialise Magics -ohjelmassa.
Toisin kuin asiaan perehtymättömät usein olettavat, 3D-tulostus (varsinkaan metallin osalta), ei ole aivan niin suoraviivaista että nappia painamalla tulisi valmis kappale ulos. Kyseessä on monivaiheinen prosessi joka vaatii laitteistojen käyttäjältä erityistä osaamista kaikissa prosessin vaiheissa. Metallin jauhepetitekniikassa tulee lisäksi ottaa huomioon työturvallisuusasiat sillä metallitulostuksen raaka-aineena käytettävä jauhe on vaarallista niin hengitettynä kuin nieltynäkin. Lisäksi jotkin yleiset tulostusmateriaalit (esim. alumiini, titaani) reagoivat hapen kanssa ja niiden varomaton käsittely voi aiheuttaa vaaratilanteita tulipalosta räjähdykseen saakka.
Seuraavassa on esitetty yleisellä tasolla alumiinin 3D-tulostusprosessin työvaiheet.
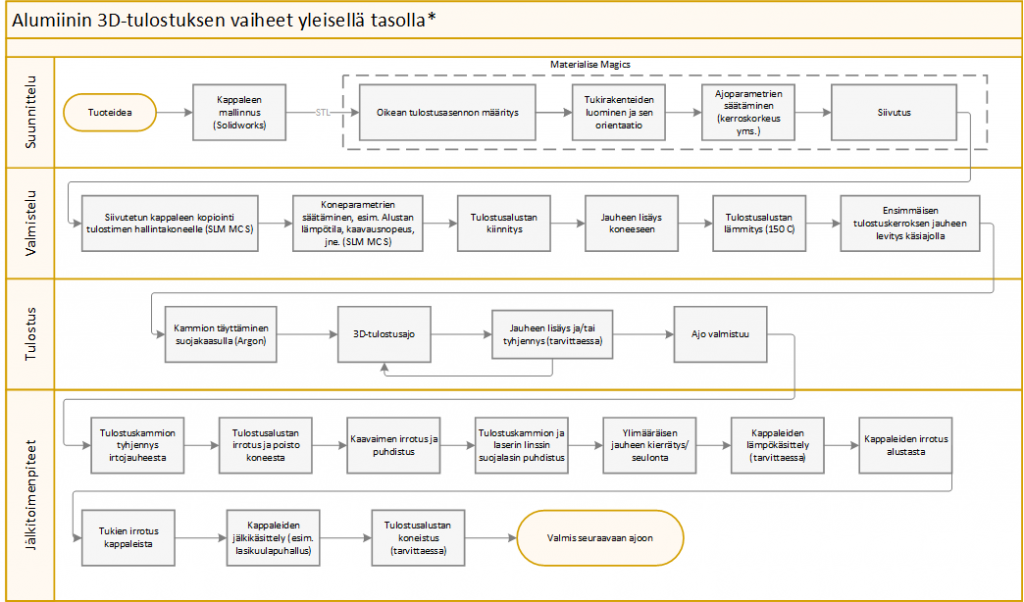
*Työvaiheiden lukumäärä ja järjestys voi vaihdella hieman valmistajakohtaisesti riippuen tulostuslaitteesta ja käytetyistä ohjelmista. Jos 3D-tulostettu materiaali vaihtuu esimerkiksi alumiinistä teräkseen, on kyseessä suurempi työmäärä sillä eri materiaalit eivät saa joutua sekaisin missään vaiheessa prosessia. Tämä tarkoittaa sekä koneen että siihen liittyvien laitteiden (3D-tulostin, seulonta-asema, atex-luokiteltu imuri) perusteellista puhdistamista.
Valmistusprosessi alkaa muun 3D-tulostuksen tapaan 3D-mallinnuksesta, joka tässä esimerkissä tehtiin Solidworksilla.
Mallinnus on usein suurin ja kallein osa tehtävää työtä, sillä 3D-tulostuksesta saa parhaan hyödyn vain silloin, kun kappale on suunniteltu 3D-tulostuksen hyödyt (ja rajoitukset) silmällä pitäen. Koska 3D-tulostusmenetelmiä on useita ja kaikilla niillä on omia erityispiirteitä, olisi mallintaessa hyvä olla jo etukäteen tiedossa se millä 3D-tulostusmenetelmällä, mistä materiaalista ja missä asennossa kappale valmistetaan. Kappale voidaan mallintaa sopivaan tulostusasentoon jo suunnitteluohjelmassa, mutta yleensä tulostusasento määritellään vasta siivutusohjelmassa.
Kun 3D-malli on tulostukseen kelpaavassa muodossa, siirretään se (yleensä STL-muodossa) siivutusohjelmaan. Tässä tapauksessa ohjelmana on Materialise Magics jossa määritetään kappaleelle sopiva tulostusasento/orientaatio ja suunnitellaan riittävä määrä tukirakenteita tulostusprosessia varten. Kappaleen tulostusasennolla on merkitystä niin pinnanlaadun kuin ylipäätään tulostuksen onnistumisen kannalta. Tulostusasennon määrityksellä pyritään välttämään suuria yhtäjaksoisia pinta-aloja ja pinta-alojen vaihteluja lämpöjännitysten ja äkillisten lämpökuormien välttämiseksi. Yleensä myös pyritään välttämään tulostusasentoa jossa kappaleen suora reuna on samassa linjassa kaavaimen kanssa jauheen tasaisen leviämisen varmistamiseksi.
Toisin kuin muovin 3D-tulostuksen jauhepetimenetelmissä, jauhepedin metallijauhe ei toimi kantavana rakenteena ja sulatettavat rakenteet vaativat tukimateriaalin, jonka päällä liittäminen tapahtuu. Yleisesti ottaen alumiinissa vaaditaan tukirakenne alle 45 asteen kulmissa. Tukirakenteella on myös kappaleen tukemisen lisäksi toinen tehtävä, sillä sen avulla saadaan johdettua lämpöä pois valmistuvasta kappaleesta.
Toisaalta tukirakenteiden poisto on yksi metallitulostuksen työläimpiä vaiheita, joten vaikka ne ovatkin välttämättömiä, tulisi niiden määrä pitää minimissään. Tukirakenteiden tarve määrittää usein paitsi tulostusorientaation, myös kappaleen geometrisia ominaisuuksia. Esimerkiksi reikien muodoissa suositaan usein pisaramaista geometriaa tukirakenteiden välttämiseksi. Alumiinin osalta pyöreiden reikien valmistaminen vaakasuunnassa onnistuu noin 10 mm asti, jonka jälkeen yläpinta alkaa roikkumaan ja menettämään muotoaan.
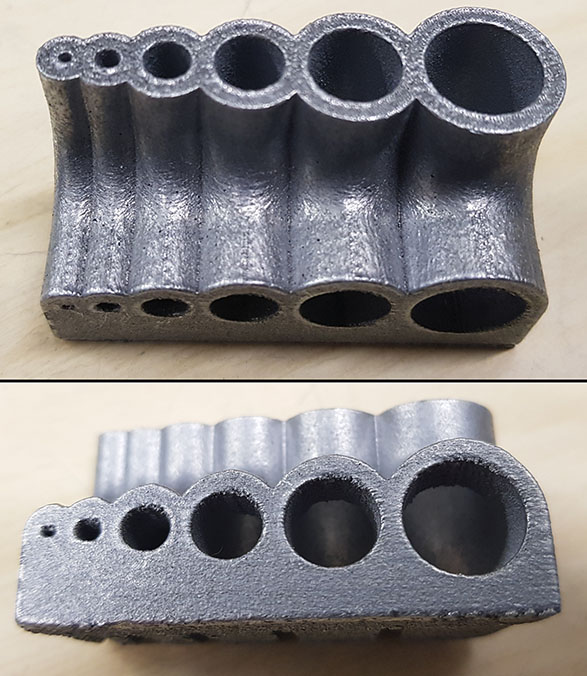
Todennäköisesti yleisin syy jauhepetimenetelmissä tulostuksen epäonnistumiseen ovat väärin suunnitellut tukirakenteet jotka repevät lämpöjännitysten voimasta irti kappaleesta tai alustasta, tai vääntävät kappaletta ei-toivottuun suuntaan. Tukirakenteiden merkitys korostuu erityisesti teräksellä ja titaanilla, mutta se tulee huomioida kaikessa metallitulostuksessa. Allaolevassa kuvassa näkyvässä testitulostuksessa havaittiin tukimateriaalin lievää repeytymistä alumiinikappaleen osalta hilarakenteen pohjalevyn osalta.
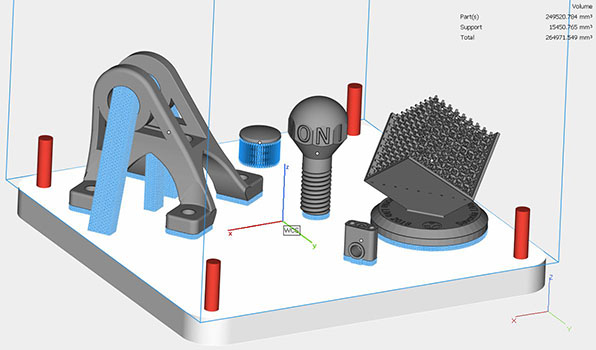
Kappaleen tulostusasennon ja tukirakenteiden määrityksen jälkeen asetetaan Magicsin puolella tulostuksen yleisiä parametreja kuten kerroskorkeus sekä käytettävät tehot ja nopeudet eri tulostuspiirteille. Kappaleiden geometria, lukumäärä ja sijoittelu vaikuttavat lopputulokseen joten parametrejä muokkaamalla on mahdollista parantaa (tai huonontaa) tulostuksen laatua ja nopeutta. Parametrien asettamisen jälkeen tehdään siivutus määritetyn kerroskorkeuden mukaisesti. Savonian testiajossa kerroskorkeus oli 30 mikrometriä.
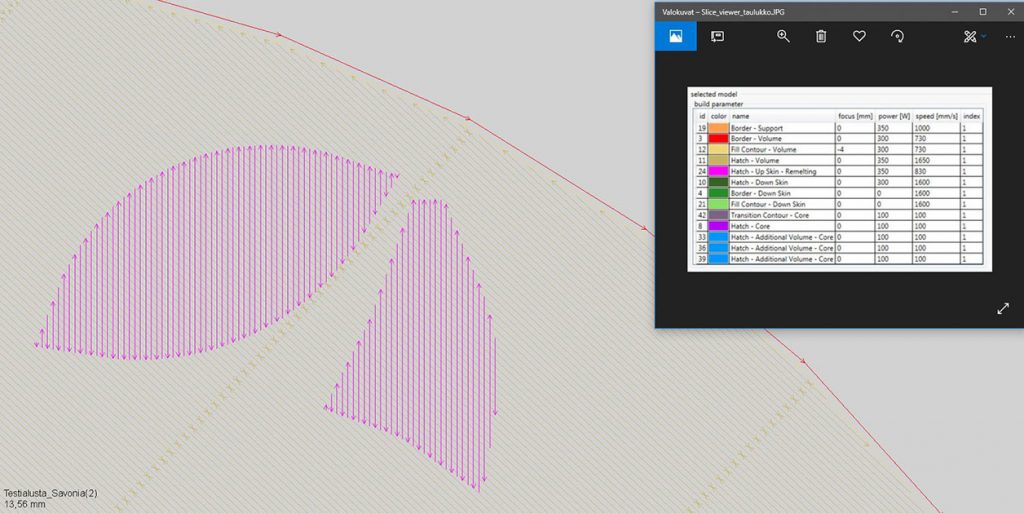
Siivutettu tiedosto kopioidaan tulostinkoneelle, jossa voidaan määrittää vielä koneparametrit kuten alustan lämpötila, kaavausnopeus, jne. Alumiinille sopiva alustan lämpötilä SLM:n laitteella on 150 C.
Siivutuksen jälkeen (tai sitä ennen) koneeseen on kiinnitettävä tulostusalusta, jolle kappaleet tulostetaan. Toisin kuin muovilaitteissa, kappaleet tulostetaan kiinteästi kiinni alustaan lämmönhallinnan parantamiseksi. Tulosteiden ja alustan väliin luodaan yleensä tukirakennetta irrottamisen helpottamiseksi. Testitulosteessa alustan väliin luotiin 4mm korkea tukirakenne. Ennen tulostusta tehtäviin vaiheisiin kuuluu myös tulostusmateriaalin lisäys mikäli koneessa ei ennestään ole riittävästi materiaalia sekä kaavaimen kalibroinnin tarkastaminen. Tämän jälkeen voidaan käynnistää tulostusalustan lämmitys. Kyseessä on paksu teräslevy joten sen lämmittäminen 150 asteeseen kestää aikansa.
Kun alusta on lämmitetty, levitetään ensimmäinen kerros jauhetta käsiajolla. Tällä pyritään eliminoimaan mahdolliset alustassa esiintyvät epätasaisuudet. Kun ensimmäinen kerros on levitetty valmiiksi, täytetään kammio suojakasulla ja varsinainen tulostus voi alkaa. Käytetty suojakaasu oli tässä tapauksessa 99,999 % puhdasta Argonia, mutta alumiinin 3D-tulostuksessa suojakaasuksi kelpaisi myös typpi. Mikäli tulostusajo on pitkä, voi olla tarpeellista lisätä materiaalia koneeseen ja/tai vaihtaa ylijäämäsäiliö kesken ajon. Kaavaimella pyritään levittämään aina varmasti riittävä määrä materiaalia, joten sitä jää hieman yli jokaisella levityskerralla.
Tulostusajon aikana prosessia voidaan seurata tulostinkoneelta tai etäyhteyden kautta. Tulostuksen aikana järjestelmä ottaa kuvan jokaisesta kerroksesta (LCS, Layer Control System) ja tallentaa sen.
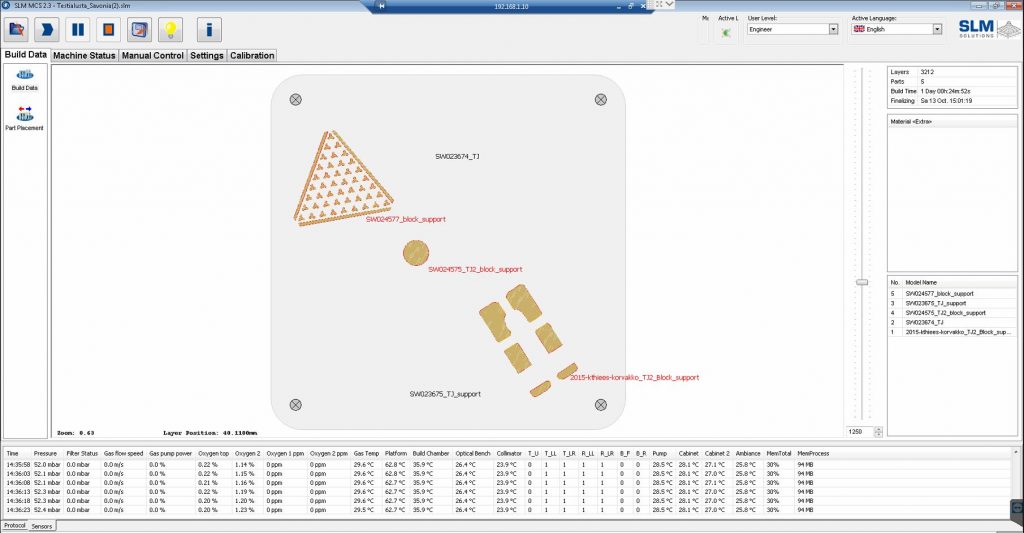
Elme Studiolla on hankittuna SLM280 3D-tulostimeen Melt Pool Monitoring (MPM) lisäosa joka mahdollistaa tulostusprosessin tarkan seurannan kerroksittain. Kerättävää monitorointitietoa voidaan tarkastella ajon aikana tai sen jälkeen. Koska tietoa tallennetaan kerroksittain (testiajossa oli 3212 kerrosta), tarkoittaa se helposti suurta datamäärää. Tehdyssä testiajossa noin 100 mm korkea tulostusajo 30 mikrometrin kerroskorkeudella kesti 24 tuntia 25 minuuttia ja siitä tallentui 80 GB verran mpm-mittadataa.
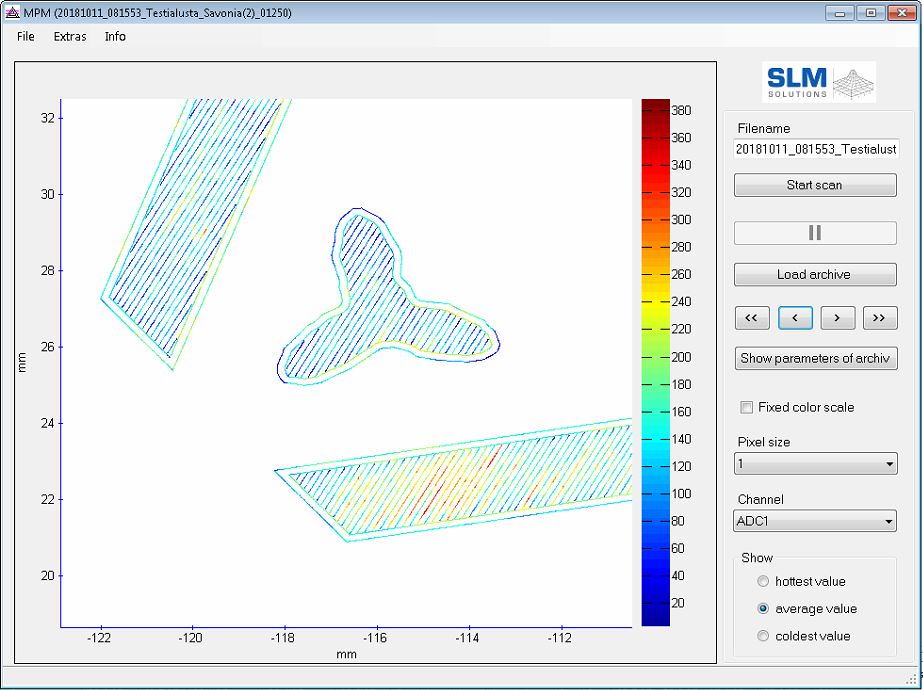
Kun ajo valmistuu, tyhjennetään kammio suojakaasusta ja jälkitoimenpiteet eli työläin osa valmistusprosessia voi alkaa.
Jälkitoimenpiteet alkavat sillä, että tulostuskammiosta tyhjennetään irtojauhe pois niiltä osin kuin se on mahdollista. Tämä tapahtuu käsityönä siten, että tulostusalustaa ajetaan ylöspäin ja samalla pensselin avulla pyyhitään ylimääräiset jauheet poistoaukon kautta poistosäiliöön. Tuotantosarjan koneissa jauheenpoisto on usein ainakin osittain automatisoitu. Tulevaisuuden koneversioissa automaatio lisääntyy muiltakin osin, mutta jauheenpoisto onnistuu tuskin koskaan täysautomaattisesti, sillä tietyt kappaleen geometriat (ja tukirakenteet) voivat estää jauheen poistamisen ennen kappaleen irroitusta alustasta.
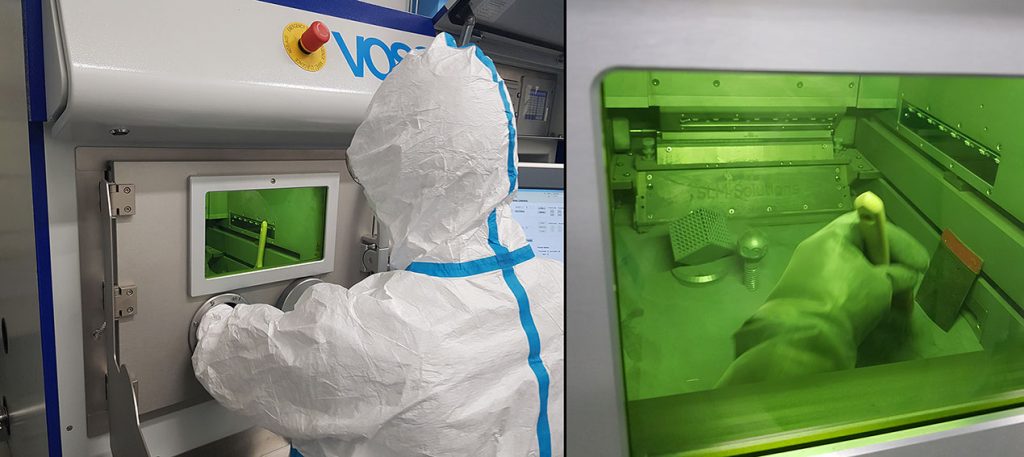
Kun suurin osa irtojauheesta on saatu siirrettyä poistosäiliöön, voidaan tulostusalusta irroittaa koneesta. Alumiinikappaleiden tulostuksessa keskikokoisilla koneilla (n. 250*250*300 mm tulostusalue) tulostusalustan paino ei nouse ongelmaksi mutta teräsosien valmistuksessa alustan poistamiseen voidaan tarvita jo apuvälineitä.
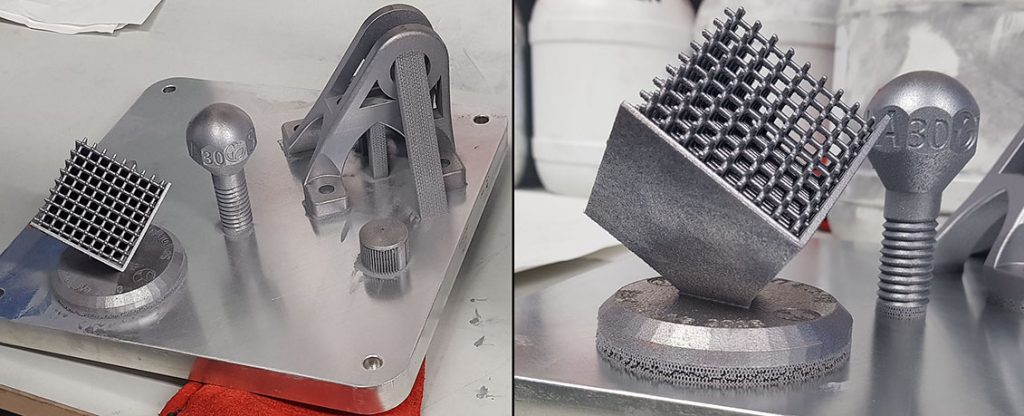
Kun kappale on irroitettu, viedään se irtojauhepöntön kanssa kierrätysasemalle sillä kappaleista irtoaa vielä runsaasti jauhetta kun alustaa voidaan vapaasti liikutella ja käännellä eri asentoihin. Ylimääräinen jauhe voidaan käyttää uudelleen kunhan se käytetään seulan läpi jossa poistetaan mahdolliset epäpuhtaudet ja liian suureksi kasvaneet partikkelit jauheen joukosta. Tässä vaiheessa voidaan myös irroittaa koneesta kaavain ja puhdistaa sekä kammio että kaavain kunnolla. Puhdistustoimenpiteisiin kuuluu myös olennaisesti laserin linssin suojalasin puhdistus ja kaavaimen pyyhkimen tarkastus (tarvittaessa vaihto).
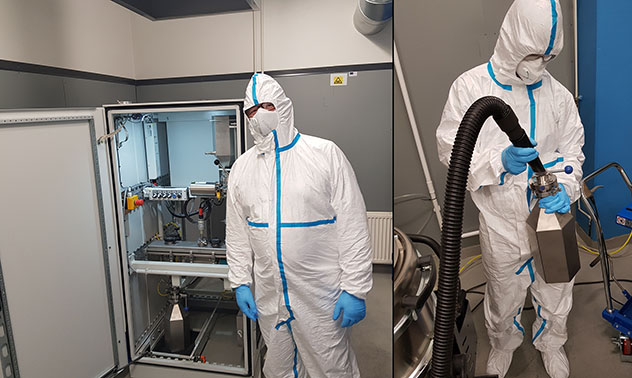
Mikäli valmistettaville kappaleille täytyy tehdä lämpökäsittely, on se usein järkevää tehdä tässä vaiheessa, kun kappaleet ovat vielä kiinni alustassa. Alumiinin (AlSi10Mg) ominaisuuksiin lämpökäsittelyn on todettu vaikuttavan seuraavasti (Lähde: University of Oulu/FMT, Tero Jokelainen, ”C3TS report 3 – Heat treatments for AlSi10Mg and 316L”, 12.1.2018):
- Myötöraja 250 Mpa -> 150 Mpa
- Murtolujuus 400 Mpa -> 300 Mpa
- Murtovenymä 1.6 mm -> 3.5 mm
Kappaleiden irroitus alustasta hoituu usein vannesahalla, lankasahalla tai puukkosahalla. Kappaleiden irroituksen jälkeen tulostusalusta puhdistetaan tulostuksen jäljistä – usein tulostusalusta koneistetaan suoraksi mutta aina koneistusta ei tarvita.
Tukien irroittaminen kappaleista voi olla hyvinkin työlästä ja haastavaa joten usein 3D-tulostuksessa mainittu ”complexity is free” (vapaasti suomennettuna jotakuinkin ”hankalat muodot ilman lisäkustannuksia”) ei pidä täysin paikkaansa metallitulostuksen osalta. Kun suunnittelussa pidetään 3D-tulostuksen rajoitukset mielessä, helpottaa se myös jälkikäsittelyvaiheita kuten tukien poistamista. On hyvä huomioida että joidenkin tukirakenteiden luominen osaksi lopullista kappaletta on valmistuskustannusten kannalta edullista, jos ne eivät haittaa lopputuotteen toiminnallisuutta.
Kun tukirakenteet on poistettu, kappale voidaan jälkikäsitellä. Yleisimpiä jälkikäsittelytoimenpiteitä 3D-tulostetuille metallikappaleille ovat lasikuulapuhallus ja mittatarkkojen pintojen koneistukset.
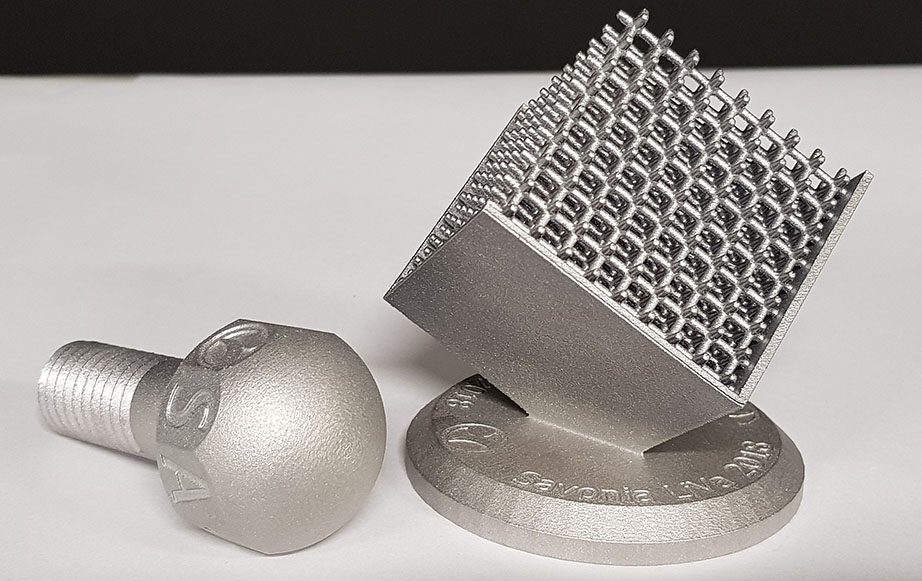
Antti Alonen
TKI-asiantuntija
Savonia-ammattikorkeakoulu

One thought on “Kokemuksia alumiinin 3D-tulostuksesta”
Comments are closed.
Kiitos mielenkiintoisesta tekstistä. 3D-tulostuksen yleistyessä eri materiaaleille turvallisuus on myös tärkeä asia. Tekstissä mainitaan Atex-imuri. Onko mahdollisesti työskentelytilassa laadittava myös Atex-räjähdyssuojaus asiakirja? Ymmärtääkseni tämä on laadittava, mikäli työskentely tapahtuu nesteiden, kaasujen tai pölyn läsnä ollessa mistä voi räjähdysvaara aiheutua.