Viime vuosien aikana markkinoille on tullut suunnitteluohjelmia, joiden toimintaperiaatteeksi kerrotaan “generative design”, eli generatiivinen suunnittelu. Niitä mainostetaan topologian optimoinnin seuraavaksi sukupolveksi ja käyttökohteina mainitaan erityisesti 3D-tulostettavat tuotteet.
Generatiivisella suunnittelulla tarkoitetaan iteratiivista suunnitteluprosessia, jossa ohjelmisto luo tietyn määrän ratkaisuvaihtoehtoja, jotka täyttävät ohjelmalle asetetut reunaehdot ja suunnittelukriteerit. Ohjelmistoa käyttävä suunnittelija rajaa vaihtoehtojen määrää säätämällä kriteerien raja-arvoja. Generatiivisen suunnittelun avulla voidaan käydä läpi suuri määrä ratkaisuvaihtoehtoja ja optimoida tulosta haluttuun suuntaan. Suunnitteluprosessin luonne myös pakottaa määrittämään suunnittelukriteerit huolellisesti ennen suunnittelun aloittamista. Tästä syystä generatiivinen suunnittelu on vaativaa ja edellyttää ainakin jonkin verran mekaniikan ja materiaalien ominaisuuksien tuntemista sillä tietokone tai tekoäly ei tee suunnittelutyötä kokonaan ihmisen puolesta tälläkään menetelmällä.
Ratkaisujen ”hyvyys” riippuu käytetystä ratkaisualgoritmista. Monesti suunnittelussa tavoitteena on toiminnallisuuden lisäksi minimoida kappaleen massa jolloin myös suunniteltavan kappaleen lujuustarkastelu on olennaista. Ainakin joihinkin generatiivisen suunnittelun ohjelmistoihin sisältyy myös lineaaristen jännitysten FEM-laskenta. Tämä voi joissain ei-kriittisissä kompakteissa rakenteissa olla riittävä, mutta suurempien, merkittävää kuormaa kantavien, riskialttiiden tai muuten kriittisten rakenteiden osalta on syytä tehdä erillinen varsinainen lujuuslaskenta suunnitellun kappaleen vaatimustenmukaisuuden toteamiseksi. Näin voidaan varmistua kappaleen kuormankanto- ja muodonmuutoskyvystä, stabiliteetista, värähtelyominaisuuksista sekä väsymiskestosta.
Savonialla testattiin Generatiivista suunnittelua Autodeskin Fusion 360 –ohjelmistolla. Testattavaksi rakenteeksi valittiin selkeän ja hyvän vertailukohdan saamiseksi kuvassa 1 esitetty fiktiivinen korvake, joka on muodoltaan ja rakenteeltaan varsin perinteinen metalliteollisuudessa käytetty osa. Savonian ALVO -projektissa testikappaleelle tehtiin topologiaoptimointi kahdella eri ohjelmistolla (PaReTo-Works ja SolidThinking Inspire). Korvake on siis myös eri optimointimenetelmien vertailun mielessä mielenkiintoinen. Allaolevassa kuvassa esitetty korvakkeen optimoitu versio on suunniteltu uudelleen kahden optimointikierroksen perusteella.
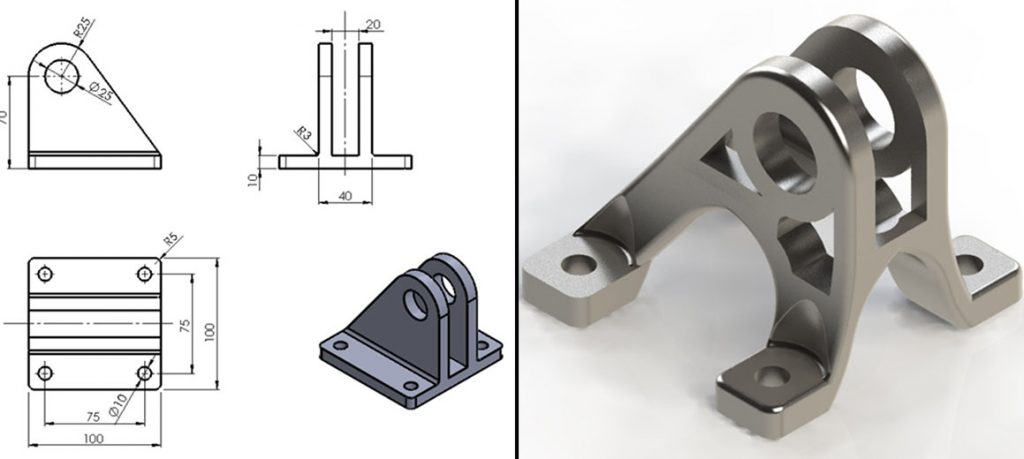
Generatiivinen suunnittelu lähtee liikkeelle määrittämällä suunnittelukriteerit. Aluksi on määriteltävä suunniteltavan kappaleen materiaali tai materiaalivaihtoehdot, valmistusrajoitteet, tarvittavat toiminnalliset piirteet (säilytettävä geometria), liittyvien osien ja työkalujen tilavaraukset (estegeometria) sekä käytettävät kuormat, varmuusluku kuormien suhteen ja reunaehdot. Kuvassa 2 on esitetty näitä suunnitteluvaiheita Autodesk Fusion 360 ohjelmassa.
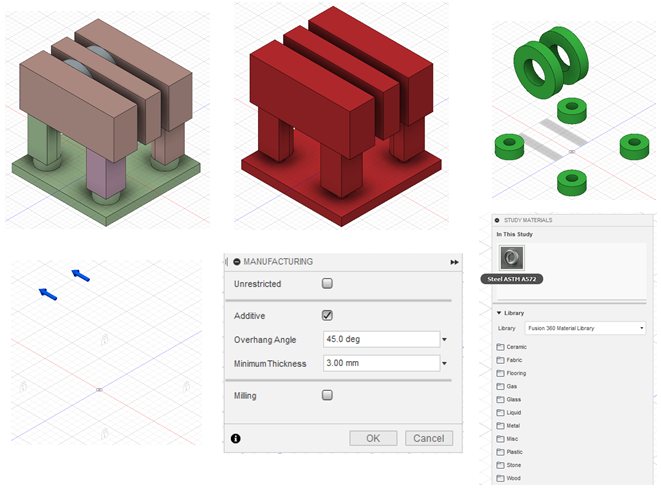
Lähtötietojen määrittämisen jälkeen suunnittelualgoritmi luo muuttujien määrän perusteella joukon ratkaisuja. Korvake-esimerkissä muuttujana on vain tulostussuunta (kappale halutaan 3d-tulostaa). Tulostussuunta X, Y tai Z suuntaan 45 asteen säännön rajoittamana eli kappaleeseen ei saa muodostua tulostussuuntaan nähden päälle kaatuvia eli negatiivisia pintoja yli 45 asteen kulmassa. Muita mahdollisia muuttujia voivat olla eri materiaalit tai eri valmistusmenetelmät omine muuttuvine rajoitteineen. Kuvassa 3 on esitetty Fusion 360 ohjelmiston pilvessä luomat ratkaisut korvakkeen muodoksi.
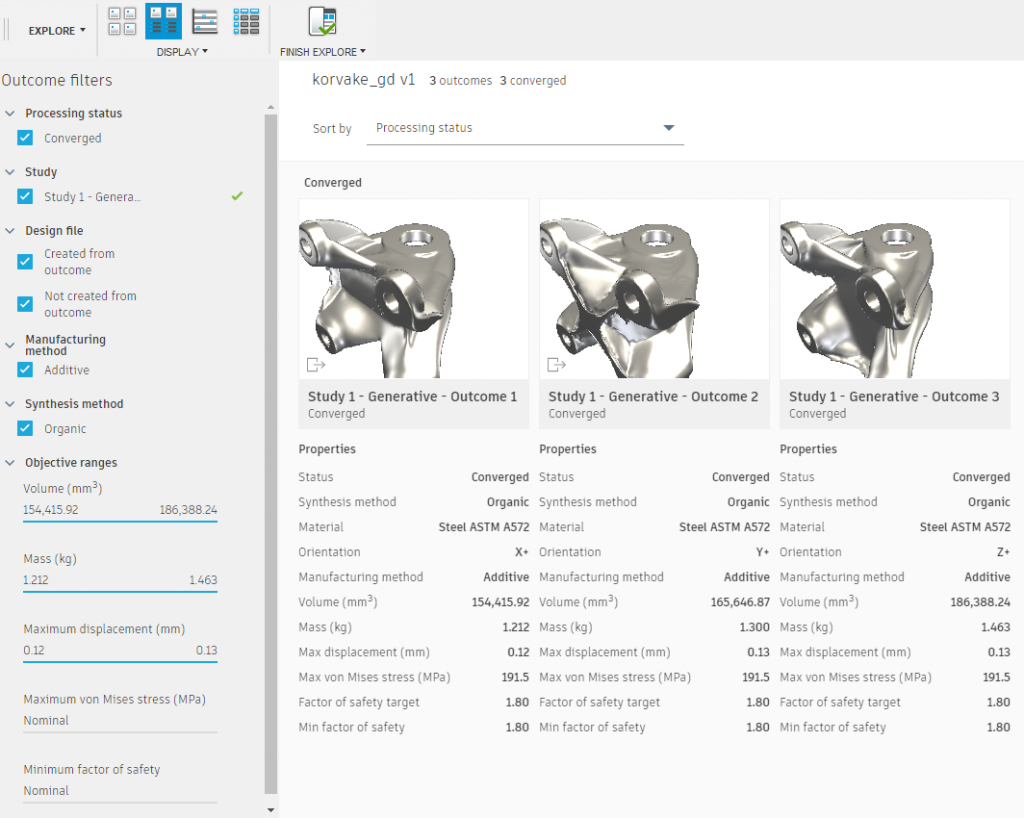
Kuvissa 4 ja 5 näkyvät ratkaisujen 1 ja 2 3D-mallit ja asetettuja kuormia vastaava lineaarisen staattisen analyysin jännitystila. Fusion 360 –ohjelmiston luomasta jännityskuvaajasta ei voida lukea paikallisia tarkkoja jännityksen arvoja, joten se on vain erittäin karkea suuntaa antava analyysi jopa lineaariseksi jännitysanalyysiksi.
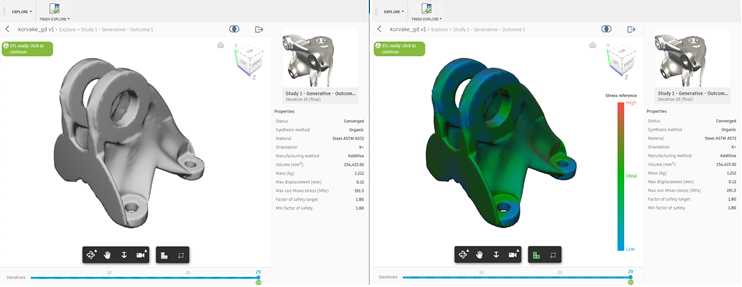
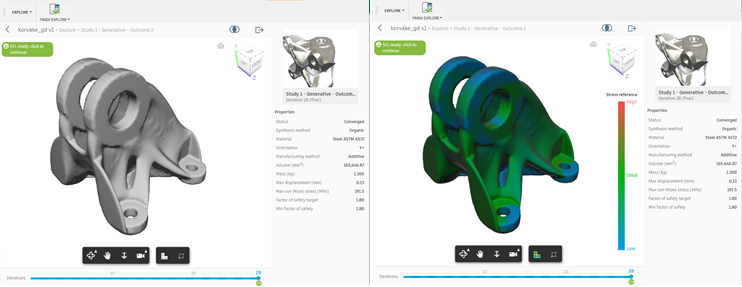
Edellämainitun testikappaleen lisäksi alla on esitelty muutama kuva ohjelman tutoriaalin esimerkkikappaleesta. Autodeskin Fusion 360 tutorial-materiaaleista löytyy harjoituksia, joiden avulla generatiivisen suunnittelun kanssa pääsee hyvin alkuun. Kuvassa 6 on esitetty eräässä harjoituksessa käytetty malli.
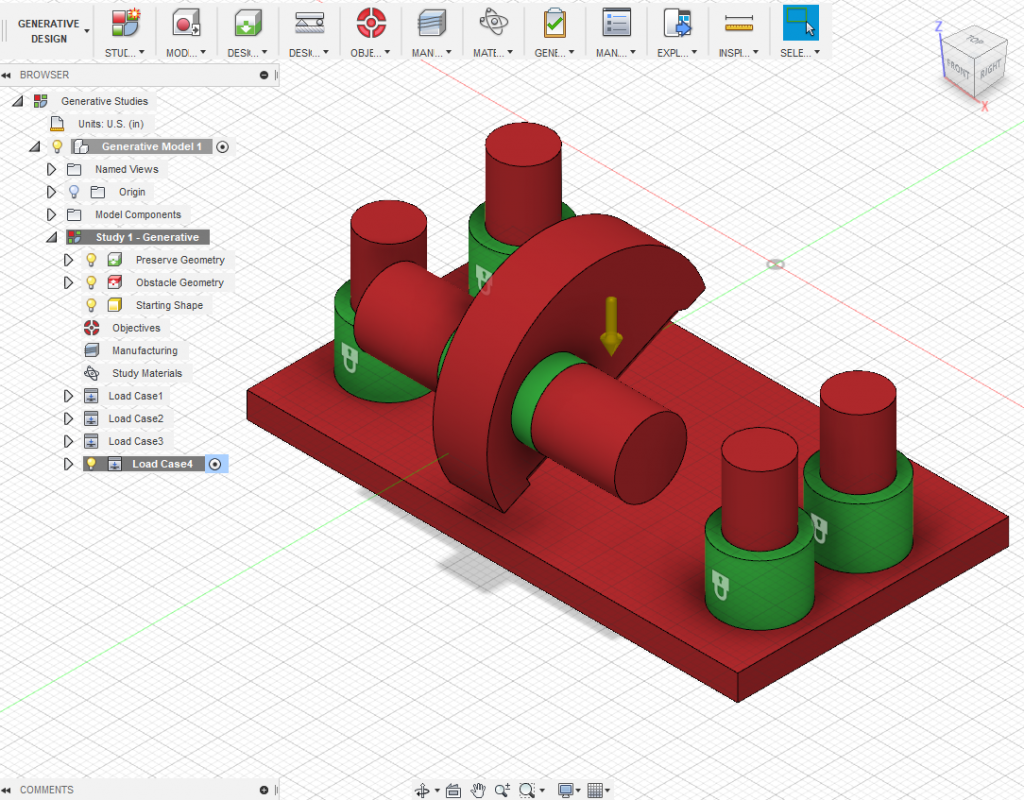
Edellä esitetyn harjoitusmallin ratkaisuksi saadaan 16 eri vaihtoehtoista muotoa. Muodot on esitetty kuvassa 8. Harjoituksessa muuttujina on neljä eri materiaalia ja neljä eri valmistustapaa (3D-tulostus X, Y ja Z suuntiin sekä rajoitteeton valmistusmenetelmä).
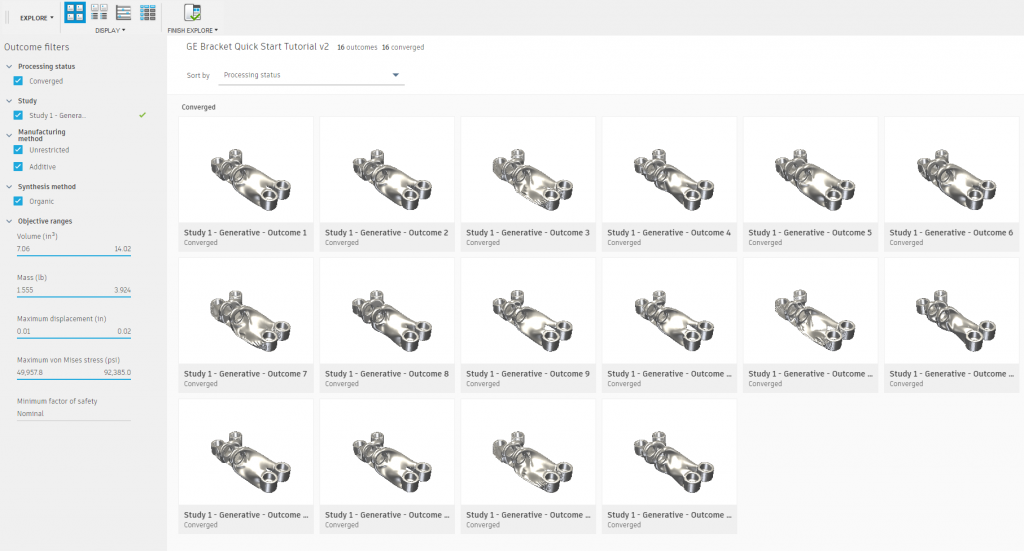
Fusion 360 ohjelmistossa on neljä erilaista tapaa tarkastella ohjelman luomia ratkaisuja: pikakuvakkeet, pikakuvakkeet ja ominaisuudet, parvikuvaaja sekä taulukko. Eri tarkastelutavoilla on helppo verrata ratkaisujen ominaisuuksia keskenään ja painottaa tai rajata tiettyjä ominaisuuksia. Kuvassa 9 esitetty ratkaisut taulukkomuodossa.
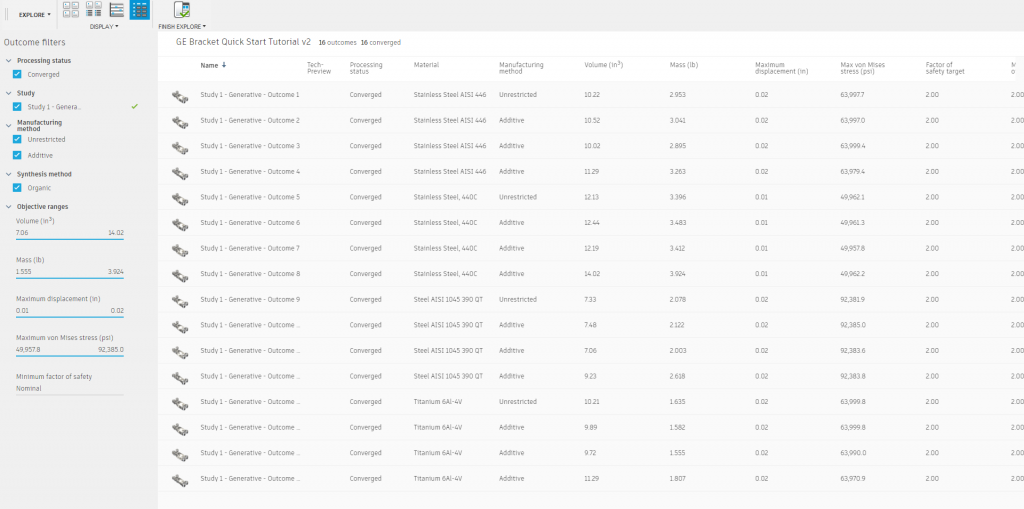
Korvakkeen ratkaisuista 1 ja 2 päätettiin tehdä myös koetulosteet Savonian 3D-tulostuslaboratoriossa. Vertailun vuoksi tulostettiin myös ALVO-projektin korvakkeet. Kaikki tulosteet onnistuivat hyvin, valmiit kappaleet on esitetty kuvissa 9 ja 10.
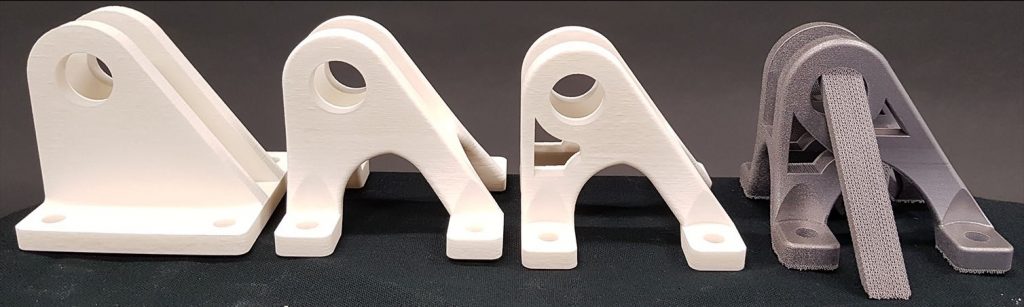
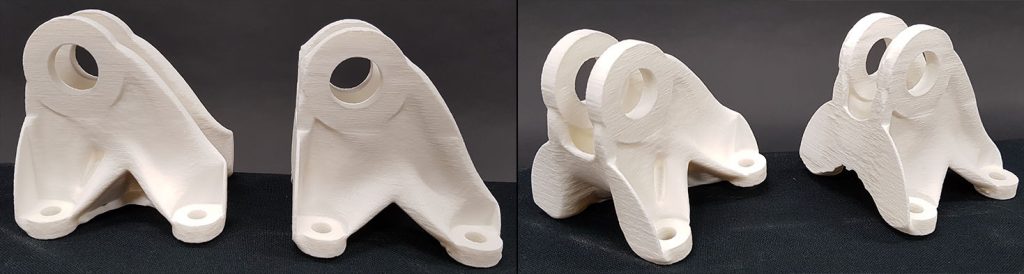
Generatiivinen suunnittelu on mielenkiintoinen lisä suunnittelumenetelmiin. Erityisesti erikoisempaa design-tuotetta suunnitellessa menetelmä on varmasti käyttökelpoinen. Myös korkean teknologian tuotteet esimerkiksi ilmailuun, avaruustekniikkaan tai huippu-urheiluun liittyen ovat potentiaalisia käyttökohteita. Näissä sovelluskohteissa kappaleen massan tai tilavuuden optimoinnilla voi olla huomattavasti suurempi merkitys kuin suunnittelu- tai valmistuskustannuksilla. Myös kalliimpien valmistusmateriaalien tapauksessa massan optimointi voi olla kannattavaa korkeista suunnittelu- ja valmistuskustannuksista huolimatta.
Menetelmä on kuitenkin monimutkainen ja työläs käyttää, joten sen käyttö yksinkertaisiin ja karkeisiin teollisuuden tuotteisiin ei ole tarkoituksenmukaista. Suunnitteluprosessin tuotoksena syntyvien kappaleiden monimutkaiset muodot puolestaan rajaavat valmistusmenetelmät käytännössä valu- ja 3D-tulostusmenetelmiin.
Simo Mäkinen
TKI-asiantuntija
Savonia-ammattikorkeakoulu

Recent Comments