Metallitulostuksen uusi aalto
Yhtenä Formnext –messujen kiinnostavimmista osa-alueista oli viime vuoden tapaan metallin 3D-tulostukseen liittyvät asiat. Metallin 3D-tulostusmarkkinat kasvoivat 2017 80% edelliseen vuoteen verrattuna. Tämän vuoden tilastoa ei luonnollisesti ole vielä saatavilla mutta messujen perusteella kasvuvauhti on edelleen kovaa.
Menossa on metallin 3D-tulostuksen “uusi aalto”, sillä itse valmistusmenetelmähän ei ole uusi asia. Jo 2000 luvun alkupuolella markkinoilla oli tarjolla laitteita useilta eri laitevalmistajilta mutta teollisuuden valmistusmenetelmänä se on kuitenkin yleistynyt ja arkipäiväistynyt vasta viime vuosien aikana. Taustalta löytyy mm. seuraavia syitä:
- Laitteiden tekniset ominaisuudet ovat parantuneet ja materiaalikustannuksetkin ovat kääntyneet laskuun saatavuuden samanaikaisesti parantuessa.
- Lopputuotekäyttöön tulevien osien sertifioinnit ja niihin liittyvät prosessit alkavat olla suurilla toimijoilla selvillä. Ilmailu- ja ajoneuvoteollisuuden toimijat sertifioivatkin kiihtyvällä tahdilla 3D-tulostettuja metalliosia yhä laajemmin käyttöön. Takana on nyt useiden vuosien kokemusta menetelmien soveltuvuudesta ja materiaalien käyttäytymisestä eli tehty tutkimus- ja tuotekehitystyö alkaa tuottaa hedelmää.
- Keskeisiä patentteja on rauennut, mikä mahdollistaa ns. ”perustekniikan” hyödyntämisen entistä suuremmalle joukolle laitevalmistajia. Metallilaitteiden laitevalmistajia kun katsotaan niin markkinoille onkin tullut runsaasti uusia toimijoita aasian markkinoilta – kilpaillen samalla tekniikalla kuin perinteiset suuret länsimaalaiset toimijat. Myös näiden ”halvempien” laitteiden laitevalmistajat tarjoavat entistä suurempia, perinteiseen jauhepetitekniikkaan perustuvia laitteita. Hinnat tosin ovat nousseet osittain jo hyvinkin lähelle länsimaisia toimijoita.
- Uudet teknologiat: Metallin 3D-tulostusteknologiat ovat pitkään perustuneet pääosin joko jauhepetitekniikkaan tai suorakerrostukseen. Markkinoilla on nyt tullut (ja edelleen tulossa) ”uusia” teknologioita, jotka tosin useimmiten perustuvat vanhojen teknologioiden parantamiseen ja niiden yhdistelyyn. Näitä ovat esimerkiksi pursotus+sintraus –kombinaatioon perustuvat laitteet Markforgedilta ja Desktop Metallilta sekä HP:n & Stratasysin kehittämät järjestelmät joiden ennakoidaan tulevan myyntiin muutaman vuoden kuluessa.
- Kappaleiden suunnitteluun käytettävät ohjelmistot ovat parantuneet ja niihin on alkanut ilmaantua ominaisuuksia, jotka helpottavat kappaleiden suunnittelua myös lisäävää valmistusta silmällä pitäen. Esimerkiksi topologian optimointiominaisuuksia on tarjolla useissa suunnitteluohjelmistoissa mahdollistaen paremmin 3D-tulostukseen soveltuvien kappaleiden tekemisen entistä helpommin.
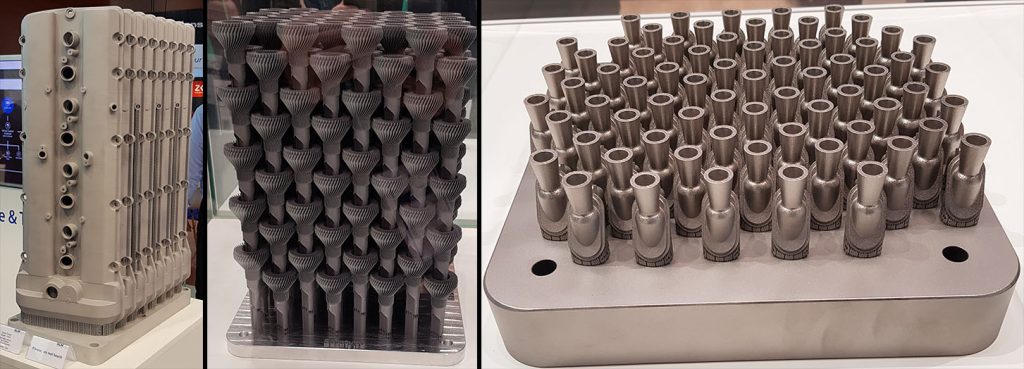
Pursotukseen ja sintraukseen perustuvat menetelemät
Yksi tämän hetken hypetyksen kohteista on pursotukseen ja sintraukseen perustuvien 3D-tulostusmenetelmien saapuminen markkinoille. Niiden on mainostettu olevan edullisempia ja yksinkertaisempia kuin jauhepetitekniikkaan perustuvat laitteet, jotka ovat teknisesti kalliita ratkaisuja niin laitteistojen kuin materiaalienkin osalta. On kuitenkin hyvä pitää mielessä että valmistusmenetelmät poikkeavat olennaisesti toisistaan joten ne eivät varsinaisesti kilpaile keskenään samoista käyttökohteista. Hieman yleistäen voidaan todeta että pursotusmenetelmä on edullisempi, mutta tulostusjäljeltään karkeampi. Jauhepetimenetelmä on puolestaan kalliimpi, mutta mahdollistaa tarkkojen ja vaativien kappaleiden valmistuksen.
Pursotus+sintraus –menetelmään perustuvien laitteiden ajatuksena on käyttää yleisemmin saatavilla olevaa MIM (Metal Injection Molding) –materiaalia ja sekoittaa se sideaineeseen. Tämä mahdollistaa pursotusmenetelmän käyttämisen kappaleen muodon luomisessa. Yksinkertaisesta toimintaperiaatteesta johtuen laitteiden valmistuskustannukset ovat jauhepetitekniikkaan verrattuna halvempia. Teknisesti prosessi menee seuraavasti:
- 3D-tulostus (3D-printing): Valmistetaan pursotusmenetelmällä kappaleen muoto tukirakenteineen.
- Sideaineen poisto (Debinding): Pesuvaiheessa 3D-tulosteesta pestään suurin osa sidosaine pois ennen sintrausta.
- Sintraus (Sintering): Kappale sintrataan uunissa lopulliseen olomuotoonsa. Lopputuloksena on tiivis (96-99%) metalliosa.
Sintrauksen aikana kappale kutistuu noin 20% joka voi aiheuttaa tietyillä geometriamuodoilla haasteita, vaikka kutistuma otetaankin automaattisesti huomioon tulostusohjelmassa.
Tukirakenteita tarvitaan paitsi pursotusmenetelmän takia, myös myöhemman vaiheen tiivistymisen vuoksi muodon säilyttämiseen. Tukirakenne pitää huolen siitä, että kappale kutistuu oikeassa suhteessa koko geometrian osalta. Nerokkaana yksityiskohtana sekä Markforged että Desktop Metalin laitteissa tukirakenteen ja kappaleen väliin tulostetaan keraamista irroituskerros, joka mahdollistaa tukirakenteen helpon irroittamisen. Sintrauksen jälkeen tiiviistä osasta voidaan napsutella tukirakenteet keraamisen irroituskerroksen ansiosta helposti pois joka nopeuttaa jälkikäsittelyvaihetta huomattavasti.
Periaatteessa samaan toimintaperiaatteeseen perustuvia ratkaisuja tarjoavat useammatkin valmistajat. Muitakin toteutuksia ja laitevalmistajia on olemassa, mutta Markforged ja Desktop Metal ovat kaupallistamisessa pisimmällä tarjoten toimivaa pakettia tutkimus-ja tuotantokäyttöön. Markforged ilmoitti toimittaneensa asiakkaille jo 100 järjestelmää, ja että vuoden 2018 loppuun mennessä on toimitettu 200 kpl. Desktop metal puolestaan kertoi että toimitukset alkavat vuoden 2019 aikana.
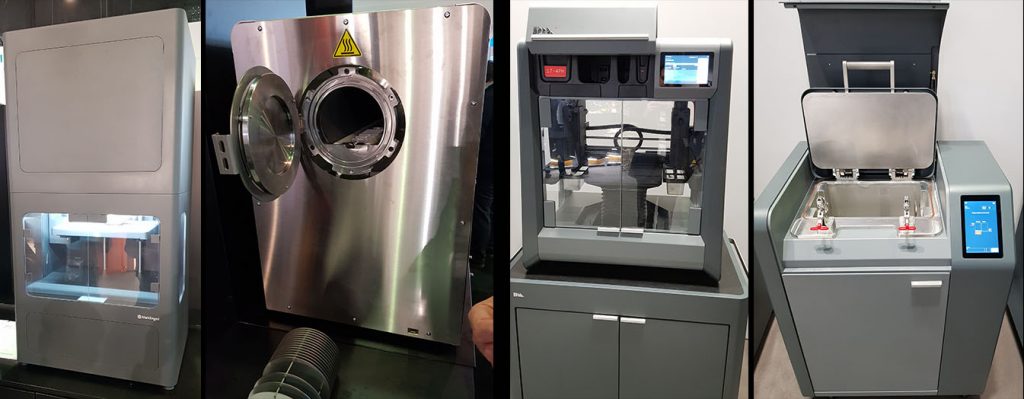
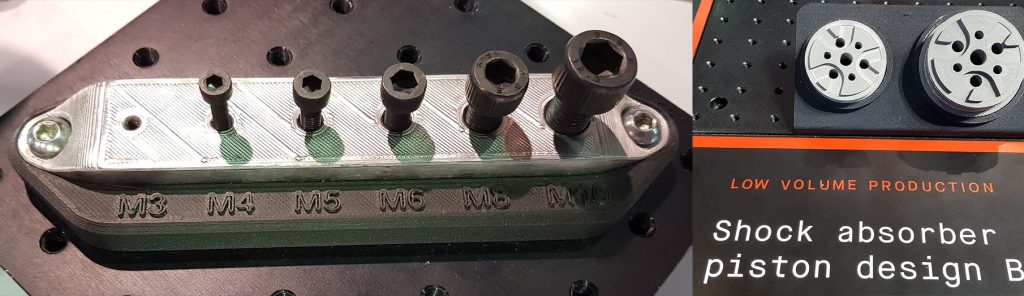
Muita uutuuksia
HP on yksi viime vuosien seuratuimpia 3D-tulostinlaitteiden valmistajia niin muovin kuin metallin 3D-tulostukseen liittyen. Yritys toi muutama vuosi sitten markkinoille MultiJet Fusion –tekniikkaan perustuvat laitteet muovin 3D-tulostukseen ja seuraavaksi on vuorossa metallitulostinten vuoro. Metallilaitteet kulkevat nimellä Metal Jet, ja niitä toimitetaan ensimmäisille asiakkaille 2020. Tulevia käyttökohteita on julkisuudessa esitelty useammankin valmistajan toimesta ja Formnext –messuilla oli ensi kertaa esillä myös itse laite.
HP on markkinoinut laitteitaan nimenomaan sarjatuotantoon soveltuviksi ja ensimmäisten asiakkaiden joukosta löytyykin sellaisia yrityksiä kuin Volkswagen, joka on ilmoittanut valmistavansa jatkossa satojatuhansia osia metallin 3D-tulostuslaitteita. Metallin 3D-tulostuksessa ei siis ole enää prototyyppit ja piensarjat, vaan painotus on uusien teknisten ratkaisujen myötä siirtymässä entistä vahvemmin myös sarjatuotannon puolelle.
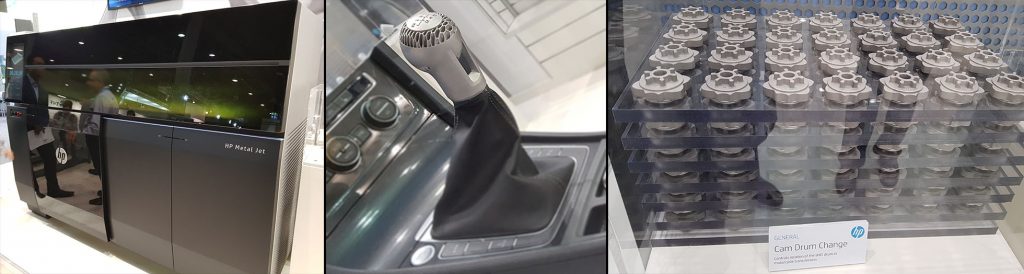
Stratasys on yksi maailman suurimpia ja vanhimpia yrityksiä 3D-tulostuksen saralla, onhan yrityksen perustaja pursotusmenetelmän kehittänyt ja patentoinut Scott Crump. Stratasys on ollut pitkään markkinajohtaja pursottavaan tekniikkaan perustuvan teollisen valmistuksen puolella, tarjoten laitteita ja tulostuspalvelua varsinkin erityismateriaaleille kuten ULTEM ja PEEK.
Nyt yritys on tuomalla ratkaisuja myös metallipuolelle. Stratasys kutsuu menetelmää nimellä LPM (Layered Powder Metallurgy), ja se tulee myyntiin muutaman vuoden kuluttua. Itse laitetta ei vielä ollut näkyvillä, mutta muiden valmistajien tapaan esillä oli menetelmällä tehtyjä esimerkkikappaleita. Menetelmä poikkeaa muutamilta osin perinteisestä sidosaineruiskutusmenetelmästä – tarkempi kuvaus laitteen toiminnasta löytyy oheisen linkin takaa: https://www.youtube.com/watch?v=tqU0U6-sAM4
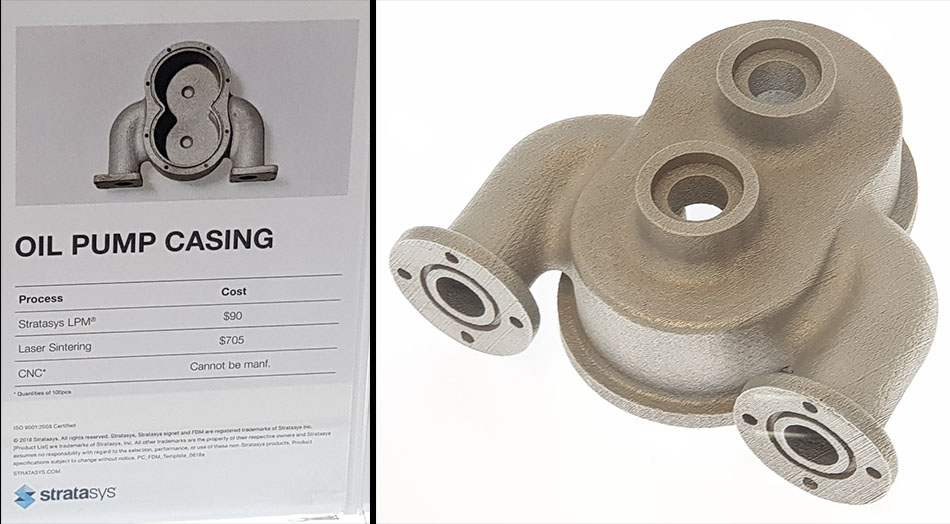
3DSystems on maailman vanhin 3D-tulostusalan yritys (perustettu 1986) joka kehitti ja toi myyntiin ensimmäisen 3D-tulostimen, SLA-tekniikkaan perustuvan “SLA-1” -laitteen vuonna 1987. Yritys keskittyi pitkään muovitulostukseen kunnes vuonna 2013 osti metallin 3D-tulostukseen erikoistuneen Layerwisen ja lähti mukaan metallitulostinten kehitykseen. 3DSystems käyttää metallin tulostustekniikastaan termiä “Direct Metal Printing”. Viime vuosina yritys on panostanut entistä enemmän myös ohjelmistopuoleen ja tarjoaa tällä hetkellä monipuolista 3DExpert –ohjelmistoa, jolla tulostusprosessia voidaan hallita alusta loppuun saakka. Lisäksi siinä on laajat ja monipuoliset ominaisuudet geometrioiden muokkaamiseen. Ohjelma vaikuttaisikin olevan varteenotettava vaihtoehto Materialisen Magics –ohjelmistopaketille.
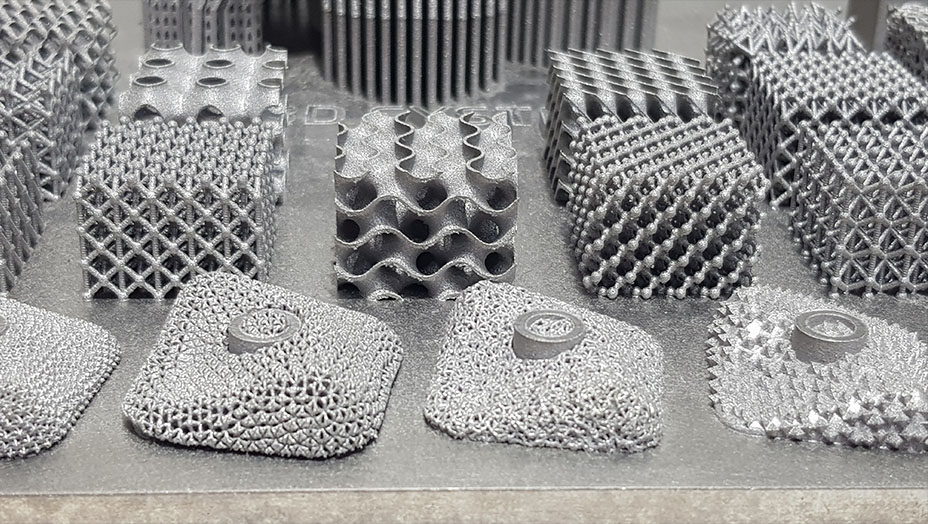
Yritys järjesti Formnextin yhteydessä muutaman tunnin seminaaritilaisuuden, jossa kerrottiin tulevista muutoksista laitekantaan. Jatkossa 3D-systems tarjoaa teolliseen tuotantoon kahta eri kokoluokan laitetta: DMP Factory 350 ja DMP Factory 500 joissa on mm. automatisoitu jauheenhallintajärjestelmä.
DMP 350 koneesta on tarjolla myös ”Flex” –versio, joka nimensä mukaisesti soveltuu joustavammin tutkimus- ja tuotekehityskäyttöön. DMP –laitteissa tulostusalue on toteutettu irroitettavan kelkan avulla joka mahdollistaa nopeamman materiaalivaihdon.
SLM päivittää 280 konesarjansa jo kolmanteen sukupolveen vuoden 2019 aikana. Kakkosversiossa parannettiin mm. tulostuskammion kaasuvirtausta, ja kolmosversion suurimpiin parannuksiin kuuluu kestosuodatin, joka nopeuttaa ja helpottaa suodattimen vaihtoprosessia. Uutuutena oli myös koneeseen liitettävä automaattinen materiaalinkäsittelyasema joka nopeuttaa tulostuksen aloitusta huomattavasti.
Kuten kilpailijoidenkin vastaavissa järjestelmissä, automaattinen materiaalinkäsittely käytännössä kuitenkin pakottaa yhden valitun materiaalin käyttöön. Vaikka koneeseen tarvittaessa pystyykin vaihtamaan toisen materiaalin, on materiaalinvaihto huomattavasti hitaampaa ja työläämpää kuin ilman materiaalinkäsittelyasemaa.
SLM:n osastolla oli esillä Divergent Blade –urheiluauton korirakenne, joka on 3D-tulostettu alumiinista ja titaanista. Runkorakenne painaa vain 46 kg, kun valmiin auton kokonaismassa on 630 kg. Yksipaikkaisessa autossa on 760 hevosvoimaa ja se kiihtyy 0-100 km 2,2 sekunnissa eli todennäköisesti kohderyhmänä ei tälläkään autolla ole lapsiperheet.
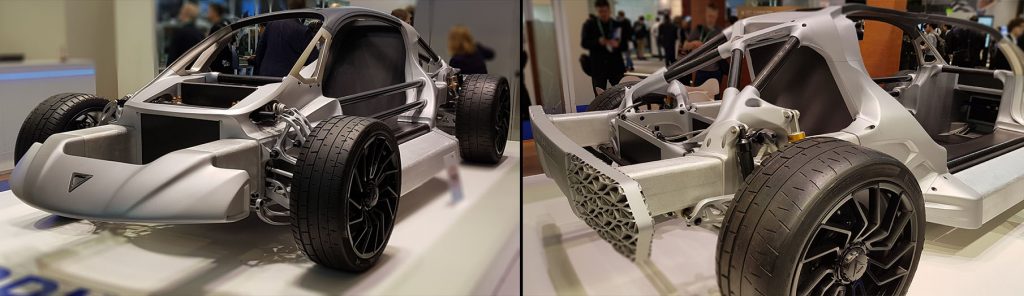
Trumpf esitteli messuilla laajan laitevalikoiman lisäksi uutta vihreään laseriin perustuvaa järjestelmää, joka mahdollistaa mm. kuparin ja kullan 3D-tulostuksen. Kupari on materiaalina haastava tulostettava heijastavasta pinnanlaadusta johtuen mutta Trumpfin ratkaisi ongelman käyttämällä vihreän laserin aallonpituutta. Yritys oli myös päivittänyt suurinta teollisen mittakaavan jauhepetilaitteistoaan (TruPrint 5000) mm. lämmitettävällä (500 °C) tulostusalustalla.
Renishawin osastolla oli esillä RenAM 500Q, yrityksen uusin teolliseen käyttöön tarkoitettu 3D-tulostusjärjestelmä joka on varustettu neljällä 500W laserilla ja melt pool monitoring –järjestelmällä.
Additive industries esitteli Metalfab1 -järjestelmäänsä uuden jälkikäsittelymoduulin, joka hoitaa samassa työvaiheessa jauheenpoiston, kappaleiden sahauksen ja tulostusalustan suoristuksen koneistamalla. Yrityksen tulostusjärjestelmän voi tällä hetkellä muodostaa seuraavista moduuleista: 3D-tulostusmoduuli 1-4 laserilla varustettuna (max. 4 kpl järjestelmässä), lämpökäsittelymoduuli, edellä mainittu uusi jälkikäsittelymoduuli, varastointimoduuli (max. 12 kpl varastossa) ja purkumoduuli.
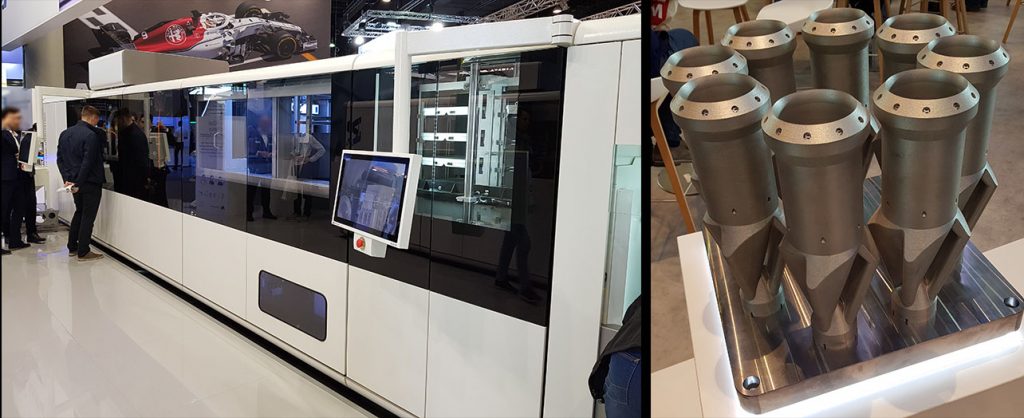
Antti Alonen
TKI-asiantuntija
Savonia-ammattikorkeakoulu

Recent Comments