3D-skannaus on 3D-tulostuksen tapaan laaja käsite jonka sisään mahtuu useita erilaisia prosesseja ja sovelluksia. Yleisesti ottaen 3D-skannauksella tarkoitetaan menetelmää, jossa kappaleesta muodostetaan virtuaalinen 3D-malli. 3D-Skannauksen menetelmiä on useita (mm. fotogrammetria, laservaloon sekä strukturoituun valoon perustuvat menetelmät).
Tässä blogikirjoituksessa keskitytään pääasiassa laserpohjaiseen, piirteiden avulla tapahtuvaan 3D-skannaukseen ja sen hyödyntämiseen 3D-tulostuksen yhteydessä. Aiemmassa blogikirjoituksessa käsiteltiin 3D-skannauksen käyttöä teollisuuden työkaluna (linkki: https://blogi.savonia.fi/3dtulostus/2018/08/28/3d-skannaus-osa-1-2-3d-skannaus-valmistavan-teollisuuden-tyokaluna/).
3D-skanneri on siis tässä tapauksessa laite, jolla tuotetaan dataa reaalimaailman kohteesta, esimerkiksi sen muodosta ja/tai ulkonäöstä. Skanneri heijastaa kohteeseen jonkin määrätyn kuvion ja kuvaa heijastetun kuvion yhdellä tai useammalla kameralla. Muotodata tuotetaan analysoimalla heijastetun kuvion muodonmuutoksia. Useat peräkkäiset muotodatat yhdistetään toisiinsa käyttämällä niissä esiintyviä yhteisiä piirteitä, esimerkiksi kohdistustarroista muodostuvia ”tähtikuvioita”.
Lopullinen skannerista ulos saatava muotodata on yleisesti mittapistepilvi 3D-avaruudessa, tai siitä luotu polygoni-pintamalli. Jotkut skannerit tallentavat lisäksi väritiedon jokaiselle mittapisteelle, jolloin skannauksesta syntyvä malli on realistinen myös värien puolesta.
Aika usein 3D-tulostuksen yhteydessä puhutaan 3D-skannauksesta menetelmänä, jolla olemassaoleva kappale voidaan kopioida. Tämä pitää kuitenkin harvoin paikkansa, sillä vaikka 3D-skannaus on hyödyllinen ja nykyisin laajasti käytetty menetelmä, on sen käytössä tiettyjä rajoitteita. Skannattavan kappaleen ulkomuodot voidaan tallentaa digitaaliseen muotoon, mutta kappaleen toimintaa tai sisäisiä rakenteita ei saada suoraan kopioitua.
3D-skannausta voidaan hyödyntää 3D-mallin luomisessa sekä kohteen 3D-mittauksessa. Sen avulla voidaan saada mittatietoa suhteellisen nopeasti ja helposti ja menetelmän käyttö on suomessakin kasvanut viime vuosina nopeaa vauhtia. 3D-mittauksessa hyöty tulee esille erityisesti silloin, kun kyseessä on perinteisin menetelmin hankalasti mitattavat muodot. Menetelmän käyttö tuotannossa vaatii usein erillisen mittausohjelmiston, jonka avulla mittadataa voidaan tarkastella tai verrata referenssimittoihin nopeasti.
Seuraavaksi käydään läpi muutama esimerkki 3D-skannauksen käytöstä 3D-tulostukseen liittyen, kun valmistusmateriaalina on muovi.
Esimerkki 1: Kipsipatsaan 3D-skannaus 3D-malliksi ja siitä eteenpäin 3D-tulostetuksi pienoismalliksi, sekä osaksi betonivalumuottia.
Tässä esimerkkitapauksessa tarkastelun kohteena oli kipsistä valmistettu patsas, jota päätettiin hyödyntää osana betonivalumuotteihin liittyvää testausta. Kipsi on materiaalina helposti 3D-skannattavaa.
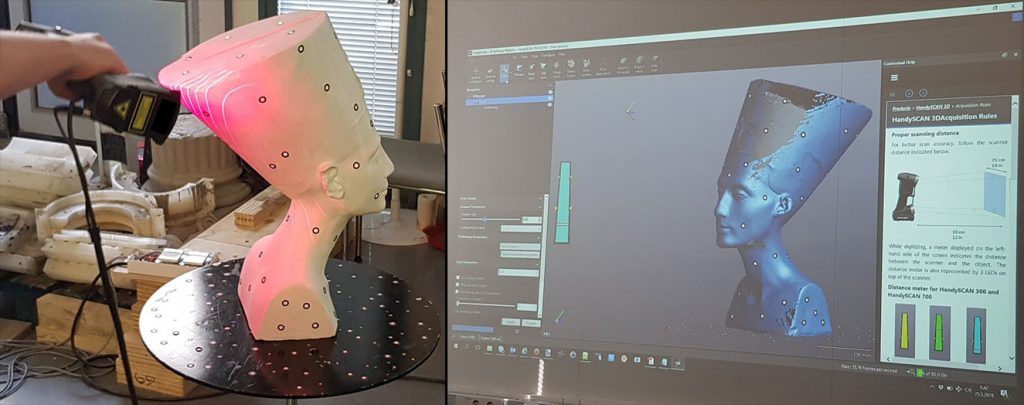
Patsaan 3D-skannaus tehtiin Creaform Handyscan 700 3D-skannerilla 1 mm mittapistevälillä. Tarvittaessa skannattuun malliin jääviä virheitä voidaan korjata suoraan 3D-skannerin mukana tulleella VX-elements ohjelmistolla skannausvaiheessa tai sen jälkeen. Tässä tapauksessa muuten täydellisesti skannatusta mallista korjattiin ohjelmistolla vain mallin pohjaan jäänyt reikä, jonka jälkeen 3D-malli tallennettiin STL-muotoon.
3D-tulostettavat kappaleet on hyvä tarkastaa ennen 3D-tulostusta pintamallissa esiintyvien virheiden varalta. Varsinkin STL-formaattiin tallennetuissa 3D-malleissa on usein erinäisiä virheitä, jotka voivat aiheuttaa valmistettavaan kappaleeseen virheitä. 3D-mallia voidaan vielä tarvittaessa korjata siihen soveltuvalla muokkausohjelmalla ennen 3D-tulostimelle viemistä. Tässä tapauksessa tarkastukseen käytettiin Netfabb Professional –ohjelmaa.
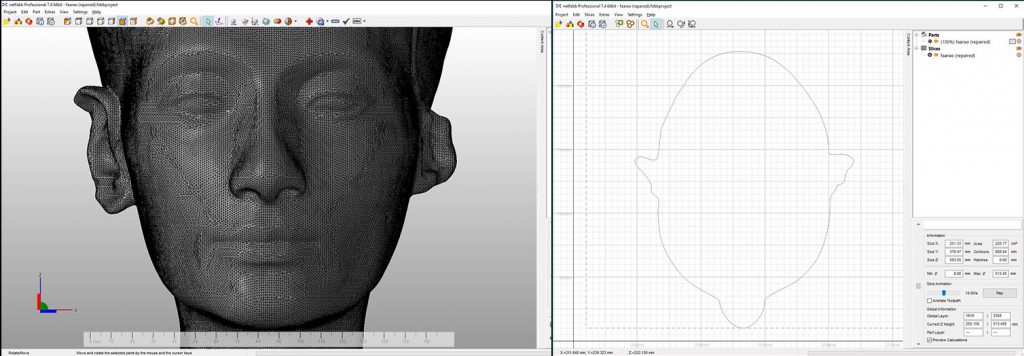
3D-skannauksen pohjalta luotu 3D-malli tulostettiin jauhepetitekniikkaan perustuvalla 3D-tulostimella (EOS P350), jota varten 3D-malli täytyy lopuksi siivuttaa 2D-kerroksiksi. Tarvittaessa mallin 2D-reunaviivoja voidaan korjata vielä 2D-kerrostasollakin. Lopuksi malli tallennetaan 2D-kerroksista koostuvassa SLI (slice layer interface) -formaatissa.
3D-tulostetun kappaleen tarkastelun jälkeen 3D-mallista päätettiin hyödyntää betonivalutestauksessa vain kasvot. Kasvoja muokattiin hieman paremmin käyttökohteeseen soveltuviksi, jonka jälkeen niistä valmistettiin pursotustekniikkaan perustuvalla 3D-tulostimella muotti. Valmistettua muottia käytettiin betonipylvään valussa.
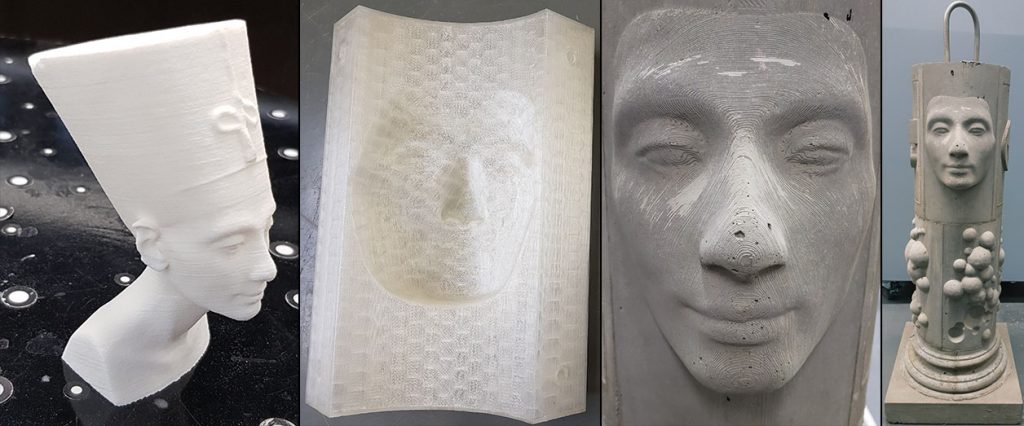
Esimerkki 2: 3D-tulosteiden valmistuksen laadunvarmistus
Lisäävän valmistuksen tunnetuimpia hyötyjä on sen soveltuvuus massaräätälöintiin. Valmistettavan tuotantoerän jokainen kappale voi olla erilainen ilman merkittävää vaikutusta valmistusprosessin toimintaan. Jokainen valmistettava kappale valmistuu geometriastaan huolimatta menetelmän mukaisessa mittatoleranssissa.
Toisaalta sama kappale pitäisi pystyä valmistamaan yhä uudelleen käyttämällä samoja tulostusparametreja, niin että kappaleen mittatarkkuus valmistuskertojen välillä säilyy muuttumattomana. Tämän esimerkin tarkoitus on havainnollistaa eroja pursotusmenetelmällä valmistettujen kappaleiden välillä. Pursotusmenetelmä on yksi yleisimmistä lisäävän valmistuksen menetelmistä.
Vaikka kappaleiden valmistuksessa käytettävä lisäävän valmistuksen menetelmä olisi sama, on eri koneiden ja laitteiden välillä eroja. Lisäksi valmistusmenetelmien toimintaan vaikuttaa suuri määrä muuttujia, joilla voi olla vaikutusta lopputulokseen. Testikappaleissa havaittuja eroja syntyi mm. käytetystä materiaalista, valmistettavien kappaleiden tulostusmäärästä (pidempi jäähtymisaika ennen seuraavaa kerrosta), käytetystä tulostimesta (erilainen siivutus, ajoparametrit, suutin, …).
Teollisuudessa edellä mainitut erot pyritään yleensä minimoimaan hyväksyttämällä kappaleen valmistus tietylle 3D-tulostinlaitteelle, ajoparametreille, eräkoolle ja materiaalille. Lisäksi varsinkin metallin 3D-tulostuksessa varmistetaan materiaaliominaisuuksien säilyminen testauksen ja mittauksen avulla.
Esimerkkikappaleen geometria on muokattu ja pienemmäksi skaalattu versio todellisesta teollisuuden kappaleesta, ja sitä valmistettiin materiaalin pursotusmenetelmään perustuvalla 3D-tulostimella (German Reprap x1000) viisi kappaletta kahdesta eri materiaalista. Suuttimen koko oli 0,8 mm, kerroskorkeutena 0,2 mm. Tulostuksen jälkeen kappaleet 3D-skannattiin ja niitä verrattiin keskenään sekä tulostuksen pohjana olleeseen STL-tiedostoon mittavirheiden havaitsemiseksi. Vertailussa käytettiin mittavirheiden värikarttaa sekä erillisiä mittapisteitä, jotka olivat sijoitettu kappaleen reunoille.
Testissä 1 materiaalina oli PLA. Testin kappaleet 1 ja 5 valmistettiin yksittäistulostuksina, kappaleet 2-4 valmistettiin samassa ajossa. Alla kuva testikappaleista tulostettuina.
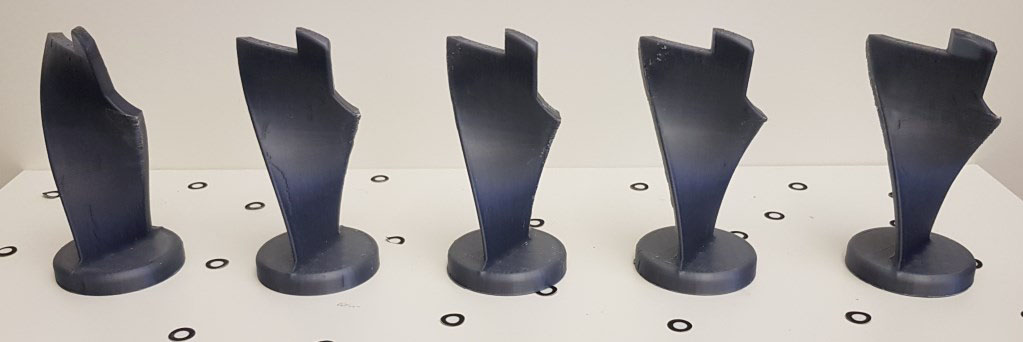
Testikappaleen geometriassa on joitakin haastavia piirteitä pursottavalle tulostukselle ja yksi selkeä ongelmakohta jonka osalta tulostusjälki oli heikompi kaikissa kappaleissa. Havaittu virhe olisi ollut mahdollista välttää oikeanlaisen tukirakenteen avulla, sillä kaareva piirre oli juuri sillä rajalla, että tukirakenne olisi tarpeen. 3D-skannaus tuo esille mittavirheinä myös materiaalin pursotusmenetelmälle tyypilliseen tapaan aiheutuvat purseet, sillä kappaleita ei jälkikäsitelty ennen skannausta.
Värikarttaa tarkastellessa on hyvä huomioida se, että värikartassa on verrattu kaikkien tulosteiden mittaeroja STL-tiedostoon sekä toisiinsa. Kun mittavirheitä yhdistetään samaan kuvaan, huomioidaan niissä vain suurimmat virheet. Mikäli samassa mittapisteessä eri kappaleiden välillä on ollut heittoja sekä plus- että miinussuuntaan, huomioidaan niistä vain toinen. Jos esimerkiksi samassa pisteessä on ollut jossain kappaleessa -1 mm heitto, ja toisessa kappaleessa +0.5 mm heitto, on se värikartassa huomioitu suuremman heiton eli -1 mm mukaan.
Polyworksissa voidaan esittää poikkeamat (mittavirheet) mm. värikarttana sekä siihen liittyvänä taulukkona, jossa kuvataan poikkeamien keskiarvo, keskihajonta sekä keskihajonnan kerrannaiset (1-6* keskihajonta). Kerrannaisilla tarkoitetaan tässä yhteydessä sitä, montako prosenttia mittauksista sijoittuu keskihajonnan alueelle. Esim. 87% mittauksista osuu 1*keskihajonta –alueelle, 96% mittauksista 2*keskihajonta -alueelle, 98% mittauksista 3*keskihajonta -alueelle, jne.
Seuraavassa kuvassa on esitetty värikartat kappaleiden väliltä sekä STL-tiedostoon verrattuna. Kuten kuvasta ilmenee, suurin osa kappaleen geometriasta toistui ongelmitta. Ensimmäisen testin kappaleiden poikkeamat referenssikappaleeseen nähden:
- Mittapisteiden lukumäärä: 13121950
- Kokonaispoikkeama: keskiarvo 0,032 mm, keskihajonta 0,096 mm (83,5% mittapisteistä, 2*keskihajonta 95,3% mittapisteistä).
- Positiivinen poikkeama: keskiarvo 0,069 mm, keskihajonta 0,095 (89,8% mittapisteistä, 2*keskihajonta 95,5% mittapisteistä).
- Negatiivinen poikkeama: keskiarvo -0,036 mm, keskihajonta 0,051 mm (87,9% mittapisteistä, 2*keskihajonta 96,2% mittapisteistä).
- Lisäksi 0,016% mittapisteistä ei mahtunut asetettujen toleranssirajojen (+/- 1 mm) sisäpuolelle.
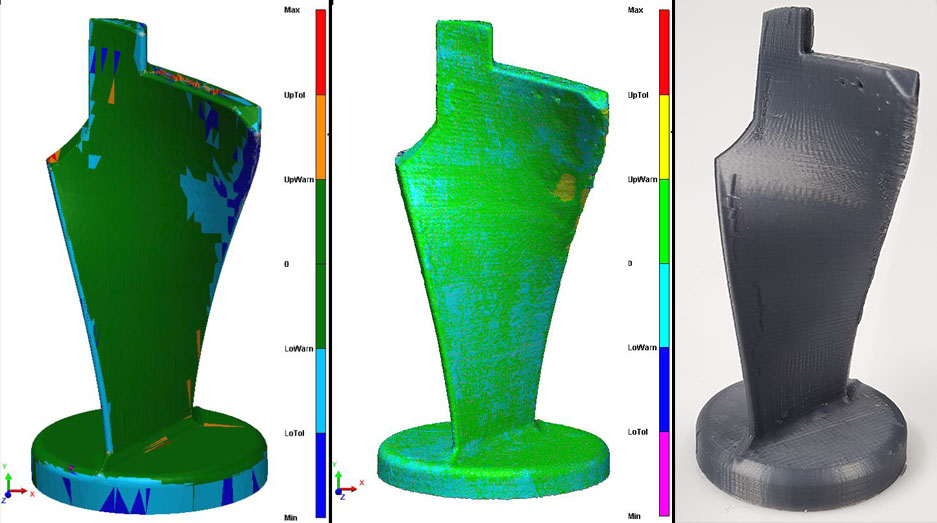
Testissä 2 materiaaliksi valittiin UPM Formi, joka on PLA –pohjainen puukuitufilamentti. UPM Formi on havaittu hyvin kantavaksi materiaaliksi joka mahdollistaa selvästi jyrkemmät tulostuskulmat kuin perusfilamentit. Puufilamentissa oleva kuitu estää materiaalin kutistumista, mutta tekee samalla materiaalista PLA-materiaalia pehmeämmän ja joustavamman. Testin kappaleet valmistettiin yksittäistulostuksina.
Testin 2 osat näyttivät silmämääräisesti tarkasteltuna hieman tulostuslaadultaan paremmilta kuin PLA –materiaalista valmistetut kappaleet, sillä selvästi näkyvien purseiden määrä oli pienempi. Toisaalta muutamat selvät virhekohdat puolestaan näyttivät hieman karkeammilta. Koska siivutus tehtiin samoilla asetuksilla, toistui kappaleissa yleisesti ottaen samat virhekohdat tälläkin materiaalilla.
Seuraavassa kuvassa on esitetty värikartat kappaleiden väliltä sekä STL-tiedostoon verrattuna. Ensimmäisessä testissä käytetyn PLA-materiaalin tapaan suurin osa kappaleen geometriasta toistui ongelmitta. Kappaleiden poikkeamat (mittavirheet) referenssikappaleeseen nähden:
- Mittapisteiden lukumäärä: 1029480
- Kokonaispoikkeama: keskiarvo -0,049 mm, keskihajonta 0,121 mm (77,7% mittapisteistä, 2*keskihajonta 97,2% mittapisteistä).
- Positiivinen poikkeama: keskiarvo 0,055 mm, keskihajonta 0,062 mm (90,8% mittapisteistä, 2*keskihajonta 98,3% mittapisteistä).
- Negatiivinen poikkeama: keskiarvo -0,108 mm, keskihajonta 0,106 mm (88.2% mittapisteistä, 2*keskihajonta 97,2% mittapisteistä). Tulosten perusteella näiden kahden materiaalien välillä ei siis ole suurta eroa lopputulokselle.
- Lisäksi 0,722% mittapisteistä ei mahtunut asetettujen toleranssirajojen (+/- 1 mm) sisäpuolelle.
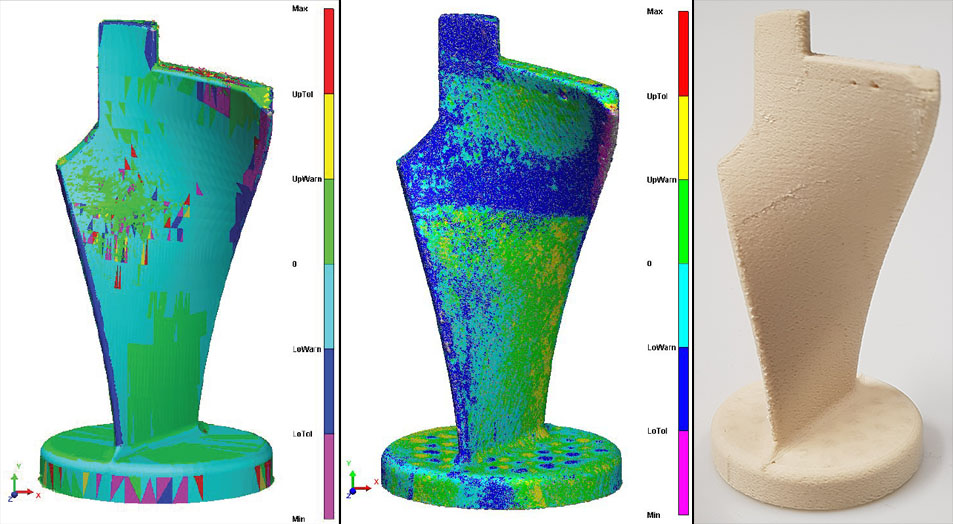
Pursotusmenetelmään liittyy ominaispiirteitä kuten purseita sekä siivutusvirheistä aiheutuvia pieniä koloja, jotka aiheuttavat helposti mittavirhepiikkejä. Näiden laatuvirheiden määrään ja laatuun pääsee vaikuttamaan tulostusparametrien kautta mutta tätä testiä varten tulostusparametreja ei lähdetty erityisemmin optimoimaan.
Mittausten perusteella voidaan todeta, että pursotusmenetelmälläkin voidaan päästä kohtuullisen tarkkaan toistojälkeen. Jauhepetimenetelmän laatutasoon ja toistotarkkuuteen ei pursotusmenetelmällä yleisesti ottaen päästä, mutta käyttökohteetkin ovat usein hieman erilaisia. Pursotusmenetelmän laaja materiaalivalikoima, pääosin edulliset laite- ja materiaalikustannukset sekä mahdollisuus suuriinkin tulostusalueisiin pitävät huolen siitä, että menetelmä säilyttää asemansa yhtenä yleisimmistä lisäävän valmistuksen menetelmistä lähitulevaisuudessakin.
Lauri Alonen
Projekti-insinööri
Savonia-ammattikorkeakoulu
Joni Andersin
Projekti-insinööri
Savonia-ammattikorkeakoulu
Antti Alonen
TKI-asiantuntija
Savonia-ammattikorkeakoulu

One thought on “3D-skannauksesta: 3D-skannaus ja 3D-tulostus”
Comments are closed.