Metallin 3D-tulostuslaitteiden myynti on kasvanut viime vuosina merkittävästi. Jauhepetitekniikan ja suorakerrostustekniikoiden rinnalle metallikappaleiden valmistukseen on nousemassa kaksi uutta menetelmää, joissa kummassakin hyödynnetään jauhemaista raaka-ainetta, sidosainetta ja sintrausta.
Pursotukseen ja sintraukseen perustuvassa menetelmässä metallijauhe on sidottuna pursotusmenetelmässä käytettävän materiaalin joukkoon. Sidosaineruiskutukseen ja sintraukseen perustuvia menetelmiä on tulossa useilta eri valmistajilta (mm. HP Metal Jet, Desktop Metal Production, Stratasys LPM), hieman erilaisina versioina. Niissä hyödynnetään jauhepetiä suuremman tuotantonopeuden saavuttamiseksi.
Tässä kirjoituksessa perehdytään pursotus+sintraus menetelmään käytännön esimerkin avulla. Pursotus+sintraus menetelmiä valmistaa tällä hetkellä kaksi laitevalmistajaa: Markforged sekä Desktop Metal. Yritykset ovat keränneet viime vuosina taakseen runsaasti suuren kokoluokan toimijoita – Markforgedin rahoittajia ovat mm. Next47 (Siemens), Porsche SE ja Microsoft. Desktop Metal on puolestaan houkutellut sellaisia yrityksiä kuin Koch, GE, GV, Panasonic, Ford ja BMW.
3D-tulostusyritysten tapaan kummatkin yritykset ovat keksineet menetelmilleen omat nimityksensä. Markforged käyttää menetelmästään nimeä ADAM (Atomic Diffusion Additive Manufacturing), eli atomidiffuusioon perustuva lisäävä valmistus. Desktop Metal puolestaan kutsuu menetelmäänsä nimellä Bound Metal Deposition, suoraan suomennettuna siis sidotun metallin sijoitusmenetelmä.
Kummatkin laitteet ovat päätoimintaperiaatteiltaan samanlaiset – laitteissa on toki pieniä eroja mutta suurimmat eroavaisuudet löytynevät ohjelmistopuolelta. Yritykset ehtivät amerikkalaiseen tapaan riidellä valmistusmenetelmien samankaltaisuuteen liittyen oikeudessakin (puolin ja toisin) ennen kuin päätyivät sovittelumenettelyyn vuonna 2018.
Käytännössä kyseessä on pursotukseen, sidosaineen pesuun ja sintraukseen perustuva valmistusmenetelmä. Raaka-aineena oleva metalli pursotetaan muotoonsa sidosaineen avulla samaan tapaan kuin muovin pursotuslaitteissa yleensäkin – pursotusmateriaalina on metallifilamentti (sidosaine, jossa on mukana metalli jauhemaisessa muodossa). Printattu kappale laitetaan pesuun, jossa osa sidosaineesta pestään pois sintraustuloksen parantamiseksi. Pesun jälkeen kappale sintrataan, jolloin siitä palaa loput sidosaineet pois jättäen jäljelle tiiviin (96-99%) metallikappaleen.
Koska tulostusvaiheessa kappale valmistetaan filamentista jossa metallijauhe on sekoitettuna poistettavaan sidosaineeseen, skaalataan kappale ohjelmassa automaattisesti n. 20% suuremmaksi ennen tulostusta. Sintrauksessa kappale tiivistyy lopulliseen kokoonsa.
Kuten kaikissa uusissa valmistusmenetelmissä, tämänkin osalta valmistajilla meni ennakoitua enemmän aikaa saada prosessi toimimaan halutulla tavalla. Muutaman vuoden odotuksen jälkeen markkinoille alkoi vihdoin saapua laitteita. Markforged aloitti viime vuoden loppupuolella toimitukset niin ripeässä tahdissa, että vuoden loppuun mennessä oli toimitettu jo 200 järjestelmää. Desktop Metal puolestaan ei ole vielä aloittanut toimituksia, mutta lupailee niiden alkavan vuoden 2019 aikana.
Suomessa Markforgedin laitteistoja jälleenmyyvät Vossi Group ja PLM Group, Desktop Metal:in laitteita Protech. Toinen suomalaisista Markforgedin jälleenmyyjistä, Vossi Group, on toimittanut Suomeen tähän mennessä kaksi järjestelmää, joista toinen on yrityksellä itsellään. Koska pursotus+sintraus menetelmään perustuva laitteisto on myös Savonian 3D-tulostusympäristön investointihankkeen hankintalistalla, kävimme tutustumassa järjestelmän toimintaan Vossin tiloissa.
Selvyyden vuoksi on painotettava sitä, että pursotus+sintrausmenetelmä ei tule syrjäyttämään jauhepetitekniikkaan perustuvia metallilaitteita vaan se täydentää 3D-tulostusmahdollisuuksia eri käyttötarkoituksiin. Menetelmät poikkeavat toisistaan niin perustoiminnaltaan kuin valmistettavien kappaleiden ominaisuuksiltaan. Kummallekin menetelmälle löytyy kysyntää, sillä valmistettavien osien käyttökohteet poikkeavat toisistaan.
Tässä vielä lyhyesti joitakin pursotus+sintraus menetelmien etuja ja rajoitteita:
Etuja
- Materiaalit: Koska menetelmä perustuu pursotukseen ja sintraukseen, ei kappaleen valmistuksessa ole samanlaisia heijastumiin tai lämpökuormiin liittyviä haasteita kuin laseriin pohjautuvissa prosesseissa. Toistaiseksi tarjolla oleva materiaalivalikoima on rajattu (ruostumaton teräs ja työkaluteräs), mutta lisää materiaaleja on tulossa (mm. Inconel 625, kupari)
- Hinta: edullinen investointikustannus jauhepetitekniikkaan verrattuna
- Käyttöturvallisuus: raaka-aine käsitellään filamenttina tai tulostuskasettina, ei jauheena
- sisäiset kennorakenteet mahdollisia
- keraaminen irrotuskerros tukirakenteen ja valmistettavan kappaleen välillä mahdollistaa kappaleen nopean irrottamisen.
Rajoitteita
- Nopeus: pursotusmenetelmän heikkoutena on yhden kappaleen valmistus kerrallaan, menetelmä ei siis sovellu nopeudeltaan sarjatuotannon työkaluksi
- Tarkkuus: skaalauksesta ja kutistumasta johtuen kappaleiden geometrinen tarkkuus ei ole samaa luokkaa kuin jauhepetimenetelmissä
Kappaleiden valmistaminen Markforged Metal X 3D-tulostuslaitteella
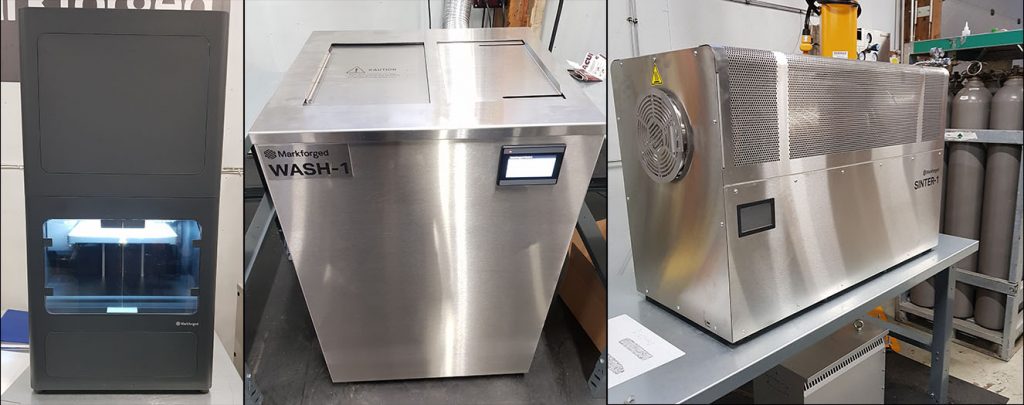
Kappaleen valmistus Markforgedin Metal X -laitteistolla voidaan jakaa toiminnallisesti neljään eri osaan. Koska kummankin yrityksen laitteistot ovat tekniikaltaan samankaltaisia, on Desktop Metal -yrityksen Studio järjestelmän valmistusprosessi hyvin samankaltainen.
- Siivutus
- Tulostus
- Pesu
- Sintraus
- Siivutus
Siivutus tapahtuu Markforgedin Eiger -ohjelman kautta. Samaa ohjelmaa käytetään kaikkien valmistajan laitteiden kanssa. Ohjelma on saatavina täysin pilvipalveluna (normaali käyttötapa), osittaisena pilvipalveluna (STL-tiedostot säilytetään paikallisesti), tai lisämaksusta myös täysin paikallisesti asennettavana versiona. Pilvipalvelupohjaiset ohjelmistot 3D-tulostuslaitteiden hallintaan ovat viime vuosina yleistyneet ja mahdollistavat raskaiden geometrioiden siivutuksen ilman tehokonetta.
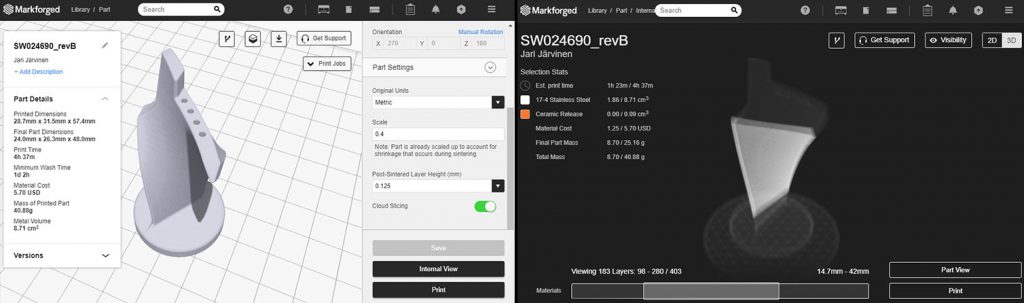
Siivutuksen yhteydessä valitaan käytetty materiaali sekä joitakin valmistuksen parametreja mutta toistaiseksi valinnat ovat hyvin rajattuja. Ohjelmistopäivitysten myötä jatkossa avautuu vaikutusmahdollisuuksia mm. Kappaleiden sisäisiin infill -rakenteisiin. Siivutusohjelma antaa arvion tulostusajasta sekä tarvittavasta pesuajasta. Pienenä yllätyksenä voi tulla pesuajan pituus joka on usein moninkertainen tulostusaikaan nähden. Tarvittavaan pesuaikaan vaikuttaa mm. kappaleen geometrian poikkipinta-ala.
- Tulostus
Tulostus on toimintaperiaatteeltaan sama kuin pursotustekniikkaan perustuvissa muovitulostimissakin. Tulostusalustan päällä on kertakäyttöinen tulostuspaperi, joka kiinnittyy alipaineella lämmitettävään tulostusalustaan. Tämä mahdollistaa kappaleen helpon irroittamisen tulostuksen jälkeen. Filamentit (sekä metallifilamentti että keraaminen irrotuskerroksen filamentti) sijaitsevat tulostimen yläpuolella kammiossa, jota lämmitetään hetki ennen tulostuksen aloittamista filamentin notkistamiseksi.
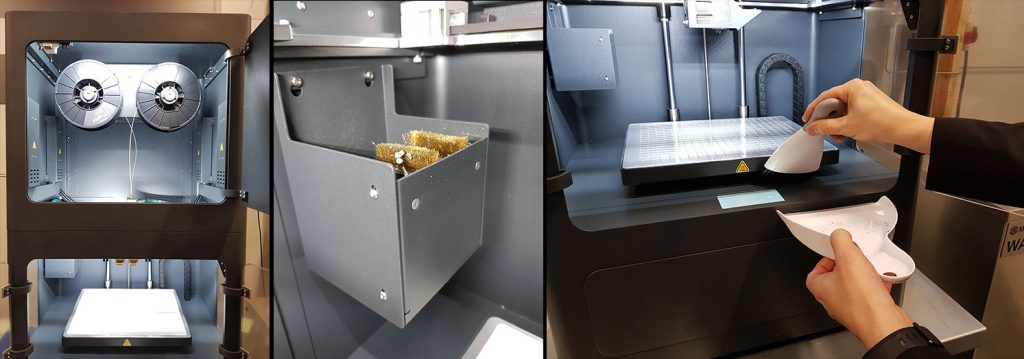
Kappaleen pohjalle valmistetaan tulostettavasta materiaalista pohjalevy, jonka paksuus on 3 mm. Tämän päälle tulostetaan lisäksi vielä tarvittavat tukirakenteet, sillä pursotusmenetelmässä tyhjän päälle tulostaminen ei ole mahdollista. Sallittu overhang näytti olevan testikappaleessamme n. 45 asteen luokkaa.
Tukirakenteen ja kappaleen väliin tulostetaan keraaminen irrotuskerros, joka on yksi pursotus + sintrausmenetelmän menetelmän parhaista puolista. Tämä mahdollistaa (ainakin periaatteessa) kappaleen irrottamisen ilman sahausta tai muuta työläämpää jälkikäsittelyä.
Tulostuksen aikana tulostuspäätä käydään puhdistamassa puhdistusasemassa lukuisia kertoja – välillä useampia kertoja kesken kerroksen tulostamisen. Pikaisesti ajatellen tulostusaseman sijaitessa vasemmassa takanurkassa kappaleen sijoituksella lähelle sitä voi säästää tulostusajassa. Tulostusaika on toisaalta nopein osa prosessia, joten sillä ei ole todennäköisesti juurikaan merkitystä läpimenoajan kannalta.
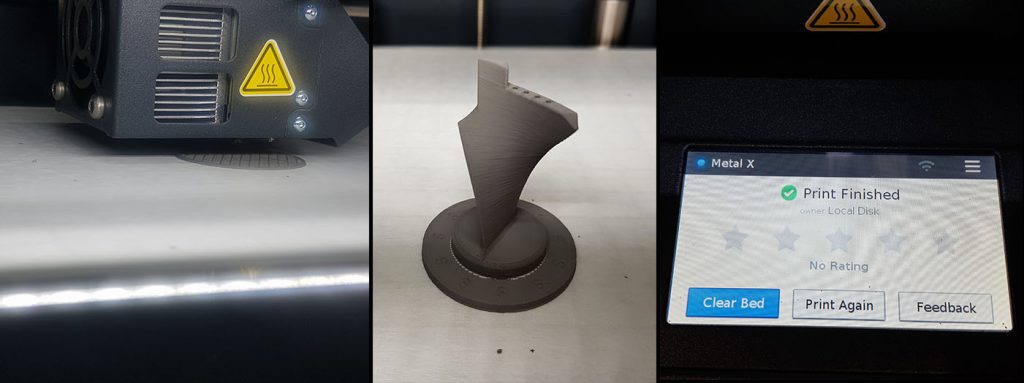
Tulostuksesta valmistuu ns. “green part”, joka on skaalattu 18,5% suuremmaksi kun materiaalina on ruostumaton teräs. Koska osalle tehdään ennen sintrausta vielä pesuvaihe, kutsutaan pesun jälkeistä osaa puolestaan ruskeaksi, ”brown part”.
- Pesu
Tulostuksen jälkeen kappaleet punnitaan ja niiden paino kirjataan ylös. Tämän jälkeen on pesuvaiheen vuoro.
Pesuvaihe kestää helposti yli vuorokauden, joten tulostimella on mahdollista valmistaa useita kappaleita, joita voidaan lisätä pesuvaiheen sekaan. Jotta pysyttäisiin kärryillä siitä missä vaiheessa pesu on minkäkin osan osalta, Eiger -ohjelmistossa voidaan syöttää pestävät kappaleet ja niille pesujen aloitusaika. Tämä mahdollistaa pesurin tehokkaan hyödyntämisen.
Kun pesuaika on suoritettu, nostetaan kappaleet hetkeksi (n. 10 min) valumaan pesualtaan yläosaan. Valutuksen jälkeen vuorossa on kuivaus pesurin toisessa kammiossa. Kuivaus kestää 4 tuntia, jonka jälkeen kappaleet punnitaan uudelleen.
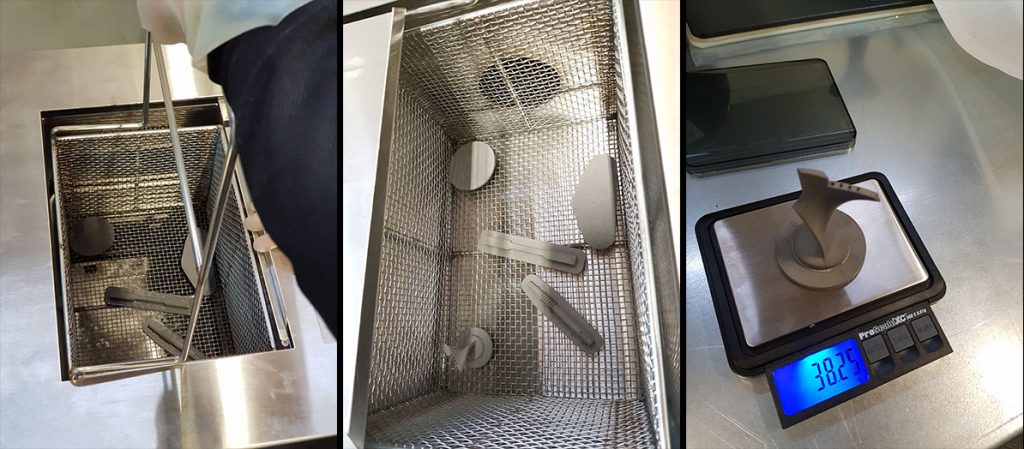
Pesuvaiheen tavoitteena on pestä pois kappaleista sidosainetta vähintään 4.2% kokonaispainosta. Koska pesuvaiheen tehokkuuteen vaikuttaa mm. kappaleen tilavuus, geometriset muodot sekä sisäiset rakenteet, ei pesuaika ole kaikille kappaleille sama. Valmistaja myös suosittelee pesemään kuppimaiset osat ylösalaisin pesun tehostamiseksi. Mikäli punnituksessa todetaan poistuman olevan alle tämän, laitetaan kappaleet uudelleen pesuun.
- Sintraus
Sintrausvaiheessa kappale tiivistyy lopulliseen muotoonsa. Valmistelevat toimenpiteet ovat suoraviivaisen helppoja, ja uunin kosketusnäytön ohjeistusta seuraamalla ne on suoritettu muutamassa minuutissa. Kappaleet laitetaan uuniin keraamisen levyn päällä. Ja ne tulee sijoittaa uuniin samassa asennossa kuin ne on tulostettu. Luonnollisesti kappaleita ei saa laittaa päällekkäin tai sisäkkäin.
Sintraus tapahtuu suojakaasussa (argon). Markforged suosittelee laitteiden käyttöön nestemäistä argonia, mutta myös kaasu näyttää toimivan. Kaasun lisäksi uunissa on suodattimia, jotka tulee vaihtaa säännöllisin väliajoin (riippuen uunin käytöstä).
Sintrausta ei saa keskeyttää aloittamisen jälkeen, eikä uunia avata kesken työvaiheen, sillä sintrauksen aikana kappaleen materiaali voi olla jauhemaisessa muodossa, jolloin se on mm. terveydelle vaarallista. Työturvallisuussyistä uunin sulkeminen ja avaus tapahtuvat kolmen pultin avulla jotka luukun sulkuvaiheessa kiristetään momenttiavaimella määrätylle kireydelle. Luukkua ei siis pysty avaamaan vahingossa.
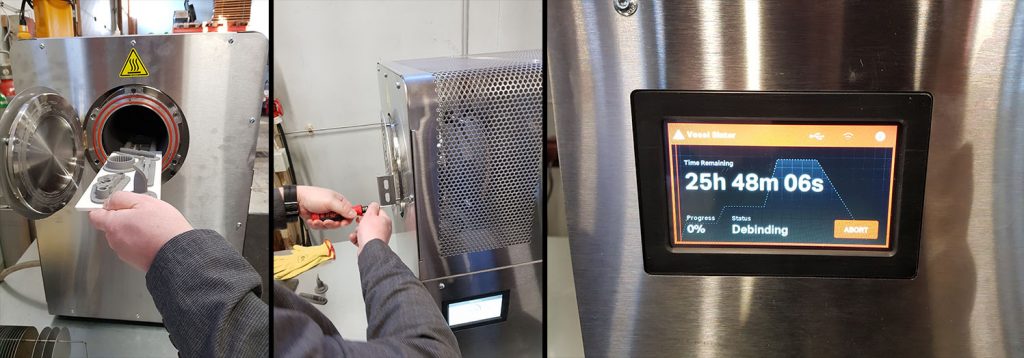
Sitrausaika on materiaalikohtaisesti vakio. Ruostumattomalle teräkselle (17-4 PH Stainless Steel) aika on 26 tuntia, riippumatta siitä miten paljon kappaleita on uunissa sisällä.
Kokonaisuudessaan valmistusaika testikappaleellemme oli n. 61 tuntia:
- Tulostusaika 4h 37 min (+ n. 1h jäähdytys, ennen kuin kappaleen sai ottaa tulostimesta pois)
- Pesuaika 26 h + valutus 20 min + kuivaus 4h
- Sintrausaika n. 26 h
Työvaiheita tarkastellessa on hyvä huomioida, että sekä pesu- että sintrausvaiheisiin mahtuu useita kappaleita samanaikaisesti.
Miten sitten on kappaleiden mittatarkkuuden kanssa?
3D-skannasimme kaksi valmistettavaa kappaletta tulostuksenjälkeisenä ”green part” -osana ja vertasimme niitä lähtötietoina olleisiin STL-tiedostoihin. Mittauksen perusteella green partit olivat 18,5% suurempia kuin STL-tiedostot, joille siivutus tehtiin. Tämä on hyvin linjassa valmistajien ilmoittaman n. 20% skaalauksen kanssa.
Sintrausajan pituudesta johtuen emme ehtineet saamaan käsiimme esimerkkikappaleena käytettyä siivekettä, joten valmiin kappaleen mittatarkkuuden arviointia varten skannasimme yhden jo aiemmin valmistuneen kappaleen, jota vertasimme tulostuksen pohjana olleeseen STL-tiedostoon.
Seuraavassa kuvassa näkyy skannatun kappaleen mittatarkkuus vain toiselta puolelta, mutta kuten lukuarvoista näkee, kappale tiivistyy hyvin mallin mukaisiin mittoihin:
- Mittapisteiden lukumäärä: 36146
- Kokonaispoikkeama: keskiarvo 0,002 mm, keskihajonta 0,069 mm sisältäen 70,9% mittapisteistä (2*keskihajonta 95,2% mittapisteistä).
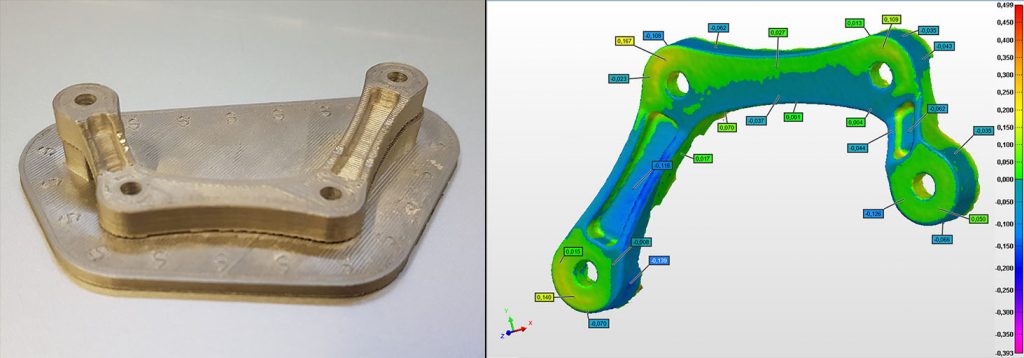
Antti Alonen
TKI-asiantuntija
Savonia-ammattikorkeakoulu
Lauri Alonen
Projekti-insinööri
Savonia-ammattikorkeakoulu

2 thoughts on “Metallin 3D-tulostus: pursotus+sintrauslaitteet saapuvat markkinoille”
Comments are closed.
Mielenkiintoista juttua!
Koska olen itse tarkastellut työurallani muutamia tuhansia poikkileikkaushieitä, lähinnä hitsauspinnoitteista, niin kiinnostaa erityisesti miten paljon on huokoisuutta tällaisissa sintraamalla tehdyissä kappaleissa. Ja tämä huokoisuus näkyisi parhaiten poikkileikkashieestä. Olettaisin että sinne jää muutama (V)% huokosia.