Tämä blogikirjoitus on julkaistu 6.7.2022 Savonia-artikkelina osoitteessa: https://www.savonia.fi/3d/savonia-artikkeli-poimintoja-firpan-vuosiseminaarista-2022-osa-2-2/
Firpan vuosiseminaarissa oli tarjolla katsaus suomalaiseen 3D-tulostusosaamiseen eri aihepiirejä sivuten. Esitykset pitivät sisällään paitsi yleistason katsausta 3D-tulostuksesta, käyttökohteista ja suunnittelusta, myös runsaasti esimerkkejä 3D-tulostuksen käytöstä Suomalaisissa yrityksissä niin muovin kuin metallinkin osalta. Artikkelin ensimmäisessä osassa käsiteltiin robottitulostukseen liittyviä asioita, tässä keskitytään muihin aiheisiin. Robottitulostukseen keskittynyt katsaus löytyy täältä: https://www.savonia.fi/artikkelit/savonia-artikkeli-poimintoja-firpan-vuosiseminaarista-2022-osa-1-2-robottitulostus/
FAME (Finnish Additive Manufacturing Ecosystem, http://www.fame3d.fi/) on nimensä mukaisesti Suomalaisten yritysten perustama ekosysteemi 3D-tulostuksen (lisäävän valmistuksen) käyttöönoton lisäämiseen Suomessa. Vuonna 2020 perustetun FAMEn tavoitteena on “Tehdä suomi ja sen yritykset tunnetuiksi 3D-tulostuksen edelläkävijöinä” mikä on hyvä mutta haastava tavoite, ottaen huomioon se, että Suomi on ainakin vielä toistaiseksi muutamia vuosia muuta Eurooppaa jäljessä niin aiheeseen liittyvässä tutkimuksessa kuin käytännön tason hyödyntämisessäkin. Mukana FAMEn perustamisessa ovat Suomen edelläkävijät niin valmistavien yritysten kuin 3D-tulostuksen palveluntarjoajienkin osalta.
Aiempina vuosina FAME on keskittynyt metallitulostukseen liittyvän tietoisuuden parantamisessa ja tänä vuonna mukaan tulevat myös polymeerien ja komposiittien tulostus. Markus Korpela kävi läpi yleisiä 3D-tulostukseen liittyviä olettamuksia / oletettuja riskejä, jotka ovat yritysten innostusta Suomessa hillinneet. Esityksessä nousi esille hyvin se, että kun käyttökohde on oikea, 3D-tulostus soveltuu myös yksinkertaisille kappaleille sekä sarjavalmistukseen.
FAMElla on meneillään DREAMS -projekti, jossa tavoitteena on nostaa kotimainen 3D-tulostusosaaminen kansainväliselle kärkitasolle vuoteen 2024 mennessä. Yksi projektin keskeisistä toimenpiteistä on kattavan ja avoimen materiaalipankin luominen, jota varten tutkitaan noin 10 000 metallista testisauvaa, jotka valmistetaan eri materiaaleista, eri 3D-tulostimilla ja eri tulostusmenetelmiä käyttäen. Tietopankin avulla korvataan alan standardien puutetta sekä helpotetaan metallien 3D-tulostamisen hyödyntämistä kaikkein vaativimmissa sovelluskohteissa, joita projektissa myös tutkitaan. Lisätietoja: https://fame3d.fi/kotimaiset-3d-tulostajat-tuottamaan-kaikkein-vaativimpia-kappaleita/
Seminaaripäivän keynotesta vastasi Edvin Resebo Amexcilta. Amexci on Ruotsalainen 3D-tulostuspalveluja tarjoava yritys (https://amexci.com/) joka on avannut tytäryhtiön Tampereelle. Aiemmin omistajilleen tutkimus- ja kehityspalveluja tarjoamaan perustettu yritys on laajentanut toimintaansa myös valmistuksen puolelle. Amexcin perustajaomistajia ovat ABB, Atlas Copco, Electrolux, FAM, Husqvarna, Höganäs, Saab, Scania, SKF, Stora Enso ja Wärtsilä.
Päivän aikana nousi esille useita huomionarvoisia asioita, joita teollisessa 3D-tulostuskäytössä olisi hyvä huomioida. Tässä muutamia poimintoja päivän keynotesta:
- 3D-tulostustuotannon skaalaus ja tuotantomäärien nosto ei välttämättä ole helppoa. Jauheeseen perustuvissa prosesseissa käsiteltävien jauheiden määrä kasvaa ja esimerkiksi jälkikäsittelyvaiheet voivat nousta pullonkaulaksi, mikäli niitä ei saada automatisoitua riittävästi. Vaikka itse 3D-tulostusprosessi onkin automaattinen, liittyy siihen vielä runsaasti manuaalisia työvaiheita. Tämä nousi esille myös muutamassa muussa esityksessä.
- 3D-tulostusprosessilla on suuri vaikutus osan materiaaliominaisuuksiin verrattuna perinteisiin valmistusmenetelmiin (esim. koneistus). Kun osa valmistetaan koneistamalla blokista, on sen materiaaliominaisuudet aika hyvin tiedossa, mutta kun sama osa valmistetaan jauheesta 3D-tulostamalla, voi tulostusprosessin aikaiset tapahtumat muuttaa materiaaliominaisuuksia hyvinkin paljon.
- Vaikka materiaalikustannukset ovat 3D-tulostuksessa kalliimpia kuin perinteisissä valmistusmenetelmissä, ovat ne vain noin 10% osan valmistuskustannuksista.
- Viime vuosina metallitulostuksessa tulostustilavuus on kasvanut ja laserien teho/määrä on noussut. Ylipäätään 3D-tulostettujen osien valmistuskustannukset laskevat lähes vuosittain.
- Kestävä kehitys ja 3D-tulostuksen ympäristöystävällisyys
- 3D-tulostuksen vaikutusta tuotteen hiilijalanjälkeen esiteltiin kolmen toteutetun esimerkin kautta. Näistä kaksi oli 3D-tulostettuna ympäristöystävällisempää, joten 3D-tulostus ei ole aina automaattisesti ympäristöystävällisin vaihtoehto.
- Hyvänä huomiona nousi esille se, että vaikka pienempi paino ja materiaalin käyttö ei toisikaan itse tuotteelle suoria hyötyjä, voi niiden merkitys kasvaa kappaleen elinkaaren lopussa, kun lasketaan hukkaan ja kierrätykseen menevän materiaalin määrää.
- Tuotteen valmistusmaalla on merkitystä, sillä co2 päästöissä on suuriakin maakohtaisia eroja jotka johtuvat energiatuotannosta. Mikäli kappale valmistetaan pohjoismaissa, on sen valmistuksessa käytetty energia tuotettu todennäköisemmin ympäristöystävällisemmin, kuin jos kappale valmistetaan esimerkiksi Kiinassa.
- Ylilaatu: Perinteiseen valmistukseen verrattuna 3D-tulostuksella tehdään usein ylilaatua joka vaikuttaa valmistusnopeuteen, kustannuksiin sekä myös ympäristöystävällisyyteen. Aika usein taustalla on se, että tulostamalla tehdään parasta mahdollista laatua koska se on mahdollista. Valmistettavien osien laatuvaatimus tulisi kuitenkin valita käyttökohteen ja tarpeen mukaan aivan samalla tavalla kuin perinteisessäkin valmistuksessa.
Metallin 3D-tulostus oli vuosiseminaarissa luonnollisesti vahvasti esillä. Delva, Valmet, Wärtsilä ja Lillbacka esittelivät metallin 3D-tulostukseen liittyviä asioita ja osaamistaan.
Valmet kertoi esityksessään teollisuusventtiileiden 3D-tulostukseen liittyvästä kehityspolustaan. Yritys valmisti ensimmäiset testikappaleet vuonna 2014, ensimmäiset asiakaskappaleet 2018 ja tänä vuonna on tulossa tuotantoon perinteisiä tuotteita korvaavia osia. Teollisuusventtiilien valmistuksen osalta jotkin 3D-tulostuksen edut, kuten paino, eivät ole relevantteja vaan päinvastoin, liian kevyet tuotteet voivat tuntua asiakkaiden mielestä heppoisilta. Yritys käyttää talon sisällä muovitulostimia prototyyppien ja konseptien valmistamiseen ja on järjestänyt työntekijöille työpajoja, joissa on kerätty ajatuksia ja ideoita siitä, miten 3D-tulostusta voisi toiminnassa hyödyntää.
Painonvähennyksellä ei siis ole teollisuusventtiileissä merkitystä, mutta jotkin muut 3D-tulostuksen hyödyt pitävät hyvin paikkansa. 3D-tulostuksen kustannusrakenne mahdollistaa yksittäiskappaleiden valmistamisen. Metallitulosteiden laatu on parempaa kuin valukappaleilla ja verrattavissa takokappaleisiin. Ala on kuitenkin vahvasti säädeltyä, joten laadunvarmistus on vielä toistaiseksi työlästä, kun 3D-tulosteille ei ole kunnollista standardointia olemassa. Ilman soveltuvaa standardia kappaleiden materiaaliominaisuudet pitää osoittaa kokein. Ennen kuin tämä puoli saadaan kuntoon, vaatii CE-merkintä liikaa työtä ja prosessi on liian raskasta useimmille tuotteilla. Tästä johtuen yritys valitsi pienen venttiilin ensimmäiseksi testikappaleeksi.
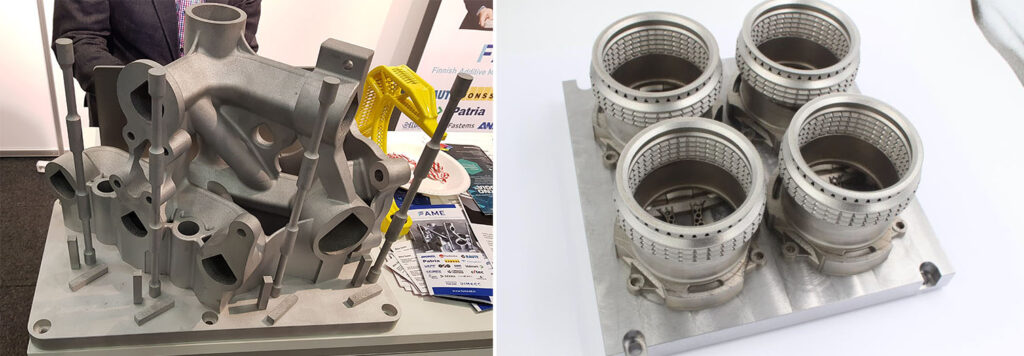
On hyvä huomata, että 3D-tulostus ei ole välttämättä sen nopeampi valmistustapa kuin muutkaan menetelmät, mikäli koko ketju valmistuksesta jälkikäsittelyyn ei ole kunnossa. Toimitusnopeuteen kun vaikuttavat myös muut mahdolliset työvaiheet kuten lämpökäsittely, koneistus ja pinnoitus.
Lillbacka puolestaan esitteli kokemuksiaan räätälöityjen erikoisleukojen valmistamisesta 3D-tulostamalla. Yritys on esitellyt aihepiiriin liittyvää osaamistaan muutamia kertoja aiemminkin ja on alalla varmasti suomen kärkeä. Yritys hankki käyttöönsä metallitulostimen 2018 ja on valmistanut sillä kolmen vuoden aikana yli tuhat kiloa 3D-tulosteita työkaluteräksestä. Yritys valmistaa hydraulisia letkuliitinpuristimia, leikkureita ja laajentimia. Puristimeen tai laajennuskoneeseen asetetaan kulloisenkin työn vaatimat leukapalat, jotka perinteisesti valmistetaan koneistamalla. Toimitusaika on 4-6 viikkoa karkaisuineen.
3D-tulostamalla haetaan nopeutta mm. prototyyppivaiheeseen sekä mahdollistetaan sellaisia muotoja, jotka koneistamalla ovat hankalia tai mahdottomia. Tulostetut työkalut ovat jo valmiiksi kovempia ja kestävät joissakin olosuhteissa vetoa paremmin kuin koneistetut. Tulostus on hyvä myös tarkkoihin pyöristyksiin, jotka voivat olla koneistamalla hankalia. Muita etuja ovat painon- ja hinnansäästö, tosin on huomattava, että tulostettu leuka ei ole aina valmistuskustannuksiltaan edullisin vaihtoehto.
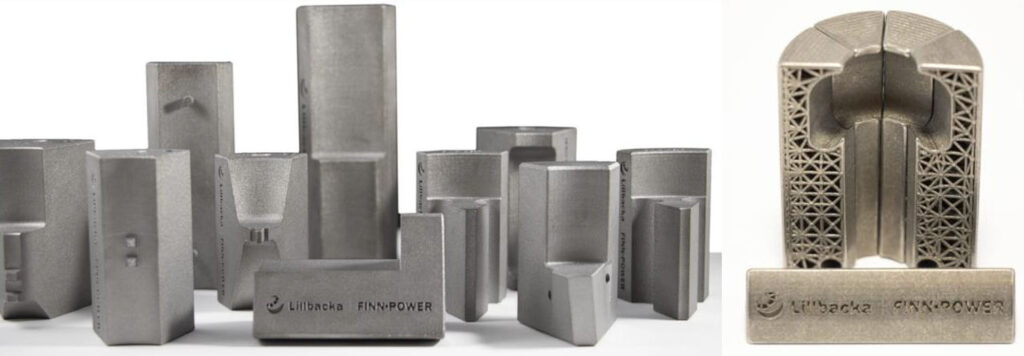
Käyttökohteesta riippuen kappale ei ole aina tulostuksen jälkeen käyttövalmis. Mikäli tulostettu kappale jälkikäsitellään esimerkiksi karkaisemalla, vaatii se 1-1.5 viikkoa työaikaa. Tämä täytyy huomioida valmistuksen läpimenoajassa.
Metallin 3D-tulostus ja lämpötilasimuloinnit
Metallin jauhepetitekniikkaan perustuvissa 3D-tulostusprosesseissa lämmönhallinta on olennainen osa onnistunutta tulostetta. Yksinkertaisissa muodoissa tämä ei nouse ongelmaksi niin helposti, mutta monimutkaisemmat muodot ja haastavammat materiaalit tuovat sen eteen väistämättä. Seminaarissa (ja yrityksen messuosastolla) oli esillä Delvan asiakascase, jossa haluttu tulosteen laatu edellytti lämpötilasimuloinnin käyttämistä. Delva (https://delva.fi/) on suomalainen metallin 3D-tulostustapalveluja tarjoava yritys.
Prosessin aikaisten lämpötilojen simulointi ja kompensointi on nykyisin suhteellisen yleistä mutta ei kuitenkaan vielä arkipäivää. Taustalla on osaamisen ja tiedon puute sekä tyypillinen hidastava este – lisenssimaksut. Ohjelmistovalmistajat ovat pilkkoneet ohjelmistojen ominaisuudet useisiin eri moduuleihin, joiden hankkiminen ja ylläpito on kannattavaa vain silloin, kun ohjelmisto on oikeasti käytössä. Kustannukset nousevat helposti yli kymmeneen tuhanteen euroon vuodessa, joten on aivan ymmärrettävää, että yritykset eivät ole halukkaita “kokeilemaan josko sillä jotain tekisi”. Pelkkä ohjelmistolisenssin kustannus voi olla 10.000 € / vuosi, johon päälle tarvitaan vielä osaava tekijä. Sivuhuomiona tähän, Savonialla kokeiltiin vuosi sitten Materialise Magicsin simulointiohjelmaa, kirjoitus siitä löytyy täältä: https://blogi.savonia.fi/3dtulostus/2021/05/14/3d-tulostettujen-metalliosien-tulostusprosessin-simulointi/
Delvan esimerkissä kyseessä oli kaivosteollisuudessa käytettävän suodatinlaitteen valmistettavuuden optimointi. Perinteisellä tavalla valmistettuna suuri osa valmistusajasta kului suodatinelementtien varusteluhitsaukseen ja hiontaan. Valmistamalla kappale 3D-tulostamalla saatiin osavalmistusta selkeytettyä ja osien määrää vähennettyä. Kappale valmistettiin aiemmin neljästä osasta leikkaamalla, taivuttamalla, hitsaamalla ja koneistamalla, kun 3D-tulostus mahdollistaa sen valmistamisen yhdellä kertaa. Toisena tavoitteena oli virtausominaisuuksien optimointi. Tyypillisesti osa valmistetaan ruostumattomasta tai haponkestävästä teräksestä.
Optimoidussa ja uudelleen suunnitellussa muodossa on parhaan tulostusasennon kannalta haastavana geometrisena ominaisuutena levymäisen rakenteen päällä olevaa massaa, joka aiheuttaa lämmön kertymistä tulostuksen aikana. Tämä aiheuttaa tulostettavan kappaleen geometrian vääntymistä tulostusprosessin aikana. Geometrian muuttaminen ei ollut mahdollista koska kyseessä on osa suurempaa kokoonpanoa. 3D-tulostettu osa laserhitsataan kiinni laserleikkeeseen, joten sen täytyy olla tulostuksen jälkeen riittävän mittatarkka. Yhtenä vaihtoehtona tässä tapauksessa olisi jälkikäsittely, esim. koneistus, mutta se ei olisi järkevää koska 3D-tulostuksella pyritään vähentämään työvaiheita.
Oikea tapa ratkaista ongelma on hyödyntää lämpötilasimulointia ja kompensoida tulevat muodonmuutokset kappaleen geometriassa. Tämä tarkoittaa kappaleen geometrian muuttamista ennen tulostusta siten, että tulostusprosessin muutosten jälkeen geometria on halutussa muodossa. Delva käytti simuloinnissa Additive Works Amphyon –ohjelmistoa (https://additive.works/), joka on nykyisin 3DSystemsin tuotevalikoimassa. Tulostuslaitteelle ajettiin kalibrointi käytetyn materiaalin kanssa ja kalibrointitieto syötettiin simulointiohjelmaan.
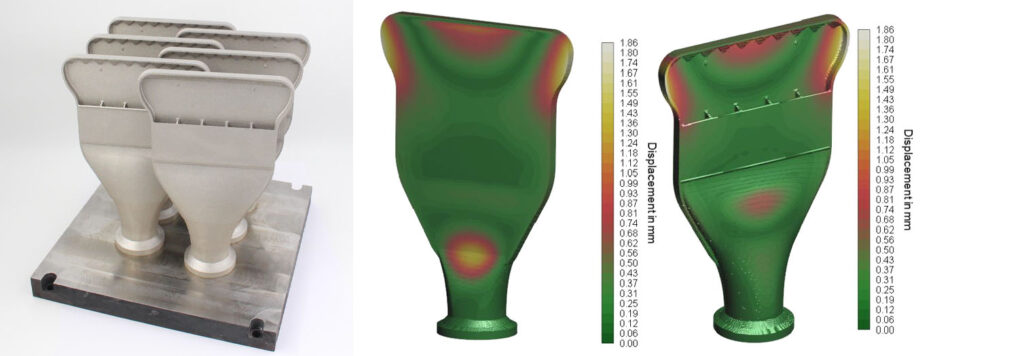
Kappaleessa on tuhansia kerroksia (kerroskorkeus 40 mikronia), joten jokaisen kerroksen simulointi tekisi mallista aivan liian raskaan toteuttaa. Tästä johtuen simulointi toteutettiin 129 kerroksen (298.000 elementtiä) yksinkertaistetulla mallilla, joka oli riittävä kompensaatiotiedon tuottamiseksi. Simulaation avulla pystyttiin tunnistamaan samat vääntymät kappaleessa mitä tuotteesta havaittiin ensimmäisten testiajojen yhteydessä. Simulaation perusteella 3D-tulostetut kappaleet valmistuivat riittävän mittatarkoiksi, jotta ne voitiin laserhitsata kokoonpanoon kiinni.
Metallitulostuksen lisäksi myös muovitulostukseen liittyvät asiat olivat seminaarissa esillä.
Wärtsilä on ollut viime vuosina yksi suomen aktiivisimmista yrityksistä 3D-tulostuksen saralla. Yrityksellä on sisäinen WHAM (Wärtsilä Hub for Additive Manufacturing) yksikkö ja se on ollut perustamassa FAME ekosysteemiä Suomeen. Juho Raukola esitteli Firpan seminaarissa, miten Wärtsilä on viime vuosina 3D-tulostusta hyödyntänyt. Numeroiden valossa hyvinkin paljon – yritys tulosti vuonna 2021 yhteensä 1353 osaa jotka liittyivät 134 projektiin. Rahalliset säästöt olivat n. 150.000 € ja ajalliset säästöt läpimenoajoissa 7 viikkoa per komponentti. Esimerkit pitivät sisällään niin muovin kuin metallinkin 3D-tulostusta mutta suurin osa tulosteista oli muovia. Maailmanlaajuisestikin asiaa katsoen muovin 3D-tulostus kattaa valtaosan kaikesta tulostuksesta, joten tämä ei ollut yllätys. Mielenkiintoisena sivuhuomiona muovitulostuksen osalta oli se että, yritys hyödyntää paljon pursotukseen perustuvia laitteita, mm. Ultimaker, Markforged Mark Two ja Markforged X7.
3D-tulostuksen eduista eri käyttökohteissa yritys esitti seuraavaa:
- Aikasäästöt: Tyypillisesti prototyypit, työkalut ja tuotannon apuvälineet
- Suorituskykyä parantavat: Monimutkaiset osat, pienet mutta kriittiset komponentit
- Rahalliset säästöt: kertavalmisteet ja työkalut & tuotannon apuvälineet
Wärtsilän esityksessä oli hyviä esimerkkejä tyypillisistä tuotannon apuvälineistä ja suojista, joita kokoonpanolinjalla käytetään. Tyypillisesti osilla oli saavutettu useiden tuhansien eurojen kustannussäästöjä, mutta sitä tärkeämpiä hyötyjiä olivat jopa kuukausia lyhyemmät toimitusajat. Työkalujen ja tuotannon apuvälineiden valmistaminen 3D-tulostamalla on aihepiiri johon Pohjois-Savon alueen yritystenkin olisi hyvä kiinnittää huomiota. Joillekin alueen suurimmista toimijoista se onkin jo tuttua mutta iso osa alueen yrityksistä ei ole vielä ymmärtänyt asian merkitystä.
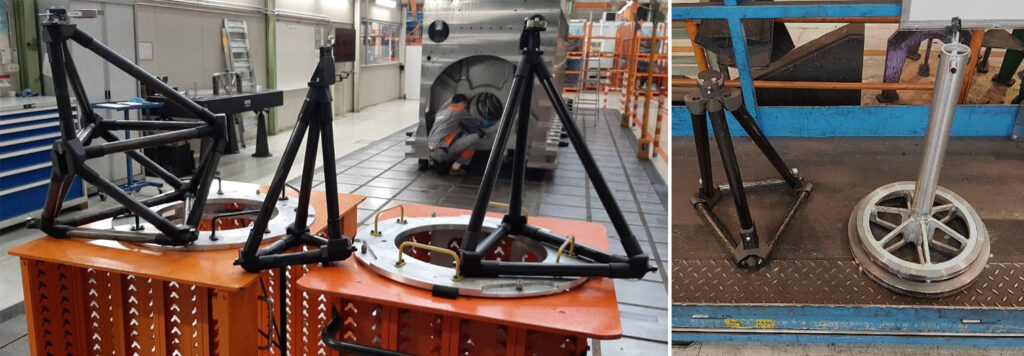
Wärtsilä on erinomainen esimerkki Suomalaisesta yrityksestä joka uskaltaa kertoa kokemuksistaan 3D-tulostuksen parissa ja levittää tietoa valmistusmenetelmän hyödyistä. Yksi suurimmista syistä siihen, että Suomi on muuta Eurooppa jäljessä 3D-tulostuksen hyödyntämisessä, on ollut kotimaisten konkreettisten esimerkkien puute. Firpan seminaari ja siellä esillä olleet yritykset vastasivat tähän tarpeeseen hyvin.
Antti Alonen
tki-asiantuntija
Savonia-ammattikorkeakoulu

Recent Comments