Heinäkuun alussa järjestettiin Digital Concrete 2020 webkonferenssi, joka toimi oivallisena tilannekatsauksena betonin 3D-tulostukseen liittyvässä tutkimuksessa. Seminaarin taustoja ja yleisiä huomioita avattiin aiemmassa blogikirjoituksessa, johon löytyy linkki tästä: https://blogi.savonia.fi/3dtulostus/2020/07/31/digital-concrete-2020-ja-betonin-3d-tulostus/
Tässä blogkirjoituksessa avataan hieman “Science meets industry” –osioiden sisältöä, sillä ne olivat mielestäni konferenssin parasta antia. Esityksissä tutustuttiin betonin 3D-tulostusta käyttävien yritysten toimintaan ja tulostusprojekteihin vuosien varrelta. Yritykset ja esitetyt projektit olivat eurooppalaisia joka tarkoittaa sitä, että kyseisiä yrityksiä ja toteutettuja projekteja koskevat samat eu-tason säännöt kuin suomeakin. On hyvä pitää mielessä että betonin 3D-tulostus on teollisuuden puolella vielä hyvin varhaisessa vaiheessa josta esitykset toimivat hyvänä esimerkkinä – olihan vanhin esitetty projekti niinkin kaukaa historiasta syövereistä kuin vuodelta 2016!
Science meets industry: De Vergaderfabriek (“the Meeting Factory”)
Esitys löytyy päivän 1 youtube -koosteesta loppupuolelta (n. 1h 50min kohdalla)
Ensimmäisessä “Science meets industry” -segmentissä tutustuttiin “maailman ensimmäiseen” 3D-tulostettuun rakennukseen jossa myös kantavat rakenteet on valmistettu tulostamalla. Projekti toteutettiin vuonna 2016 ja sitä esitteli Witteveen en Bos. Yritys on sittemmin toteuttanut useita rakennusprojekteja, joissa on käytetty betonin 3D-tulostusmenetelmiä ja sillä on Singaporessa käytössään etelä-aasien suurin betonin 3D-tulostusrobotti.
“The meeting factory” on kokoushuone, jonka osalta asiakkaat haastoivat teollisuutta käyttämään uutta tekniikkaa ja rakentavan pyöreän kokoushuoneen joka soveltuu ympäristön arkkitehtuuriin. Rakennus sijaitsee lentokentän lähellä, joten arkkitehti suunnitteli kokoushuoneen siten, että ilmasta käsin se muistuttaa lentokoneen suihkumoottorin muodostamaa ilmapyörrettä. Tästä johtuen kaikki kokoushuoneen seinät ovat kaksoiskaarevia. Projektin aikana jouduttiin tekemään muutoksia alkuperäisiin muotoihin, jotta siitä saatiin rakenteellisesti kestävä.
Rakennuksen seinät muodostuvat neljästä kerroksen paksuisesta betonitulosteesta. Näistä kolme kerrosta muodostavat kantavan rakenteen ja neljäs kerros visuaalisen ulkorakenteen. Seinäelementtien sijoittamisen jälkeen niiden pohjalle valettiin noin 30 senttimetriä valubetonia jolla seinät kiinnittyvät pohjaan. Lämmöneristys toteutettiin täyttämällä seinäelementit biopohjaisella eristevaahdolla. Kuva seinäelementin rakenteesta näkyy kuvassa 3 oikealla.
Vuonna 2016 markkinoilla oli vain yksi, CyBen valmistama betonin 3D-tulostuslaitteisto, joka oli liikuteltavan alustan päälle asennettu käsivarsirobotti. Laitteella ei kuitenkaan voinut liikkua ja tulostaa samaan aikaan vaan sen käyttö vaati pysäyttämisen, asemoinnin ja kalibroinnin. Noin kolme metriä leveän yksittäisen seinäelementin tulostus kesti 2 tuntia, mutta tulostuslaitteen liikutus ja asemointi uudelle paikalle kesti 6 tuntia
Rakennus valmistettiin paikan päällä suojateltassa, ja viranomaishyväksyntää varten seinäelementit valmistettiin “design-by-testing” menetelmällä, joka tarkoitti niiden kuormitustestausta 1:1 kokoisina siihen saakka, kunnes rakenne saatiin hajoamaan. Viimeisimmän version kohdalla testausjärjestelmä ei enää kyennyt rasittamaan seinäelementtiä hajoamispisteeseen.
Kyseessä oli ensimmäinen 3D-tulostettu rakennus, joten rakentamisen aikana tuli vastaan lukuisia haasteita. Esimerkiksi tulostusmateriaalin pidempiaikaisesta käyttäytymisestä ei ollut tietoa, mutta näin muutaman vuoden jälkeen siinä on havaittu vain pieniä kutistumia uloimmassa visuaalisessa kerroksessa. Muita haasteita olivat mm.
- 3D-tulostettu betonielementti ja paikallaan valettu betoni reagoivat hieman keskenään aiheuttaen tummemman kerroksen tulostettuun betoniin.
- Nopeasti kuivuvan betonin 3D-tulostaminen ulko-olosuhteissa oli haastavaa, vaikkakin tulostus tapahtui suojateltassa. Osa tulostetuista elementeistä halkeili ja jouduttiin tekemään uudelleen.
- Digitaalinen työnkulku ja sama digitaalinen malli tulisi olla kaikkien osapuolten käytössä: Projektissa suunnittelijat, arkkitehti ja suunnitteluinsinöörit työskentelivät parametrisen mallin kanssa, kun taas elementit valmistanut yritys työskenteli toisen mallin kautta – tämä oli aiheuttanut pieniä muutoksia rakennusvaiheessa suunnittelumalliin verrattuna.
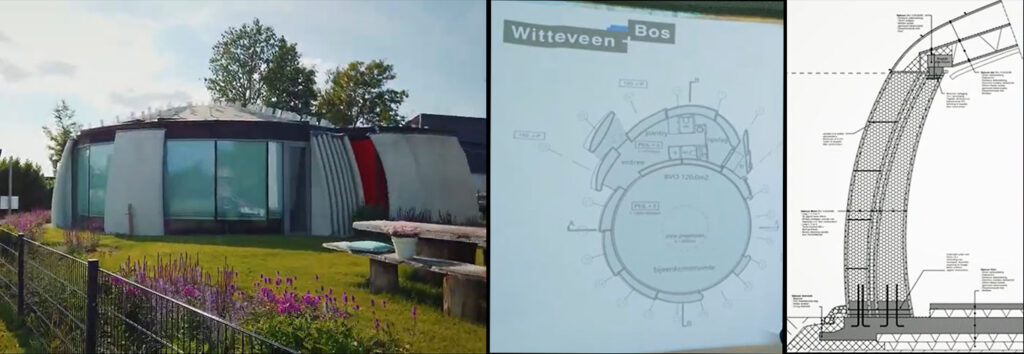
Science meets industry: “Project Milestone”
Project Milestonen esitys löytyy 2.päivän youtube -koosteesta loppupuolelta, mutta siitä löytyy myös erillinen video jonka linkki on seuraava: https://www.youtube.com/watch?v=HhQz83IFgqs
Projektissa rakennetaan yhteensä viisi asuintaloa, joista osassa on useampi kerros. Rakentaminen aloitetaan yksikerroksisesta rakennuksesta, jonka kattorakenne on puuta. Tulostettavassa seinärakenteessa ei käytetä teräsvaijeria betonitulostuksen aikana vaan se on suunniteltu siten että vaijeria ei tarvita. Myöhemmissä rakennuksissa kattorakenteet voivat olla myös vahvistetusta betonista tulostettuja elementtejä.
Betonielementit valmistetaan tehtaalla, ja toimitetaan paikan päälle. Logistiikan osalta kuljetusta pyritään helpottamaan valmistamalla tehtaalla betonilaattoja, jotka ovat osa rakennusten perustuksia. Laattoja käytetään hyväksi kuljetuksessa, eli tulostetut betonielementit kuljetetaan laattojen päällä rakennustyömaalle.
Kuten monissa muissakin betonin 3D-tulostusprojekteissa tällä hetkellä, betonin sideaineena käytetään normaalia portlandsementtiä, sillä se on materiaalina tuttu. Toisaalta sille on tyypillisenä haasteena 3D-tulostuksessa se, että kovettumisaika on noin 90 minuuttia. Elementin korkeuden ja kerrosmäärän kasvaessa alimmat kerrokset eivät ehdi kovettua riittäväksi kantaakseen rakennetta. Toisaalta hitaan kovettumisajan ansiosta betonilla on helpompi saavuttaa monoliittinen rakenne eli kerrosten välinen sidos on rakenteeltaan samanlaista kuin kerroksissakin.
Projekti valmistuu vuonna 2021. Yrityksen edustajan mukaan kyseessä ei ole enää proof-of-concept rakennus vaan tällä hetkellä ollaan teknisissä valmiuksissa tasolla 7 tai 8. Valmistusmenetelmän hyödyntämisessä ollaan kuitenkin vielä alkuvaiheessa, josta johtuen yritys mainitsi muutamia haasteita, joista osa on ilmeisesti ehditty jo ratkaisemaan.
- Koska kyseessä on pysyvät asuinrakennukset, tulee rakennusluvat luonnollisesti olla kunnossa. Tämä on ratkaistu tiiviin viranomaisyhteistyön ja materiaalitestauksen avulla.
- Ulkoseinän pinnanlaatu on 3D-tulostuksessa kerroksellista. Tämä ei kuitenkaan ole aina sitä mitä halutaan.
- Elementtien tulostusajat ovat pitkiä, jopa 16 tuntia per elementti.
Tässäkin esityksessä yrityksen edustajat kertoivat, että haluaisivat vaihtaa portlandsementin ekologisempaan vaihtoehtoon. Toinen aiempia esityksiä myötäilevä asia oli kiinnostus tukirakenteiden automaattiseen lisäämiseen. Yritys haastaakin tutkimuslaitoksia kehittämään menetelmiä, joiden avulla tukirakenteet saadaan sijoitettua tulostuksen aikana automaattisesti.
Rakennusten pitäisi valmistua vielä tämän vuoden aikana. Lisätietoja projektista löytyy mm. osoitteista: https://3dprintedhouse.nl/en/ ja https://www.witteveenbos.com/projects/first-3d-printed-concrete-houses/
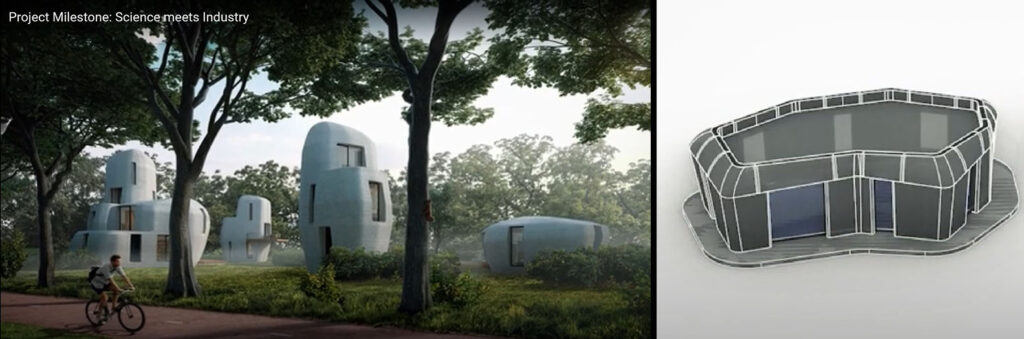
Science meets industry: Bam & siltarakenteiden 3D-tulostus
Siltoihin ja portaisiin liittyvä “Science meets industry” -esitys löytyy myöskin 2.päivän youtube -koosteesta. BAM on yksi Alankomaiden suurimmista rakennusalan yrityksistä, joka on perehtynyt betonin 3D-tulostukseen jo useamman vuoden ajan.
Esitelty siltaprojekti on noin 8 metriä pitkä jalankulkusilta, joka otettiin käyttöön 2017. Silta tulostetiin Eindhovenin teknillisen yliopiston laitteilla ja tiloissa. Koska kyseessä oli yrityksen ensimmäinen tulostamalla valmistettu betonisilta, projektissa pidettiin taustalla myös valmiutta sijoittaa paikalle normaalitavalla valmistettu silta.
Sillan kantokyky ja kestävyys todistettiin valmistalla silta “design-by-testing” menetelmällä – tarkoittaen kuormitustestausta 1:1 kokoluokassa. Sillassa käytettiin teräsvaijeria vahvikkeena – vaijeri sijoitettiin tulostuksen aikana tulostuspään yhteydessä sijaitsevan lisälaitteen avulla. Lisäksi kokoamisvaiheessa siltaan lisättiin jälkijännitetyt tukiraudat. Kaiken varmistamiseksi yritys teki vielä toisen kantokykytestin sen jälkeen, kun silta oli sijoitettu paikalleen. Valmistamisessa noudatettiin rakentamisen eurocodeja, ja silta täyttää kaikki vaadittavat viranomaismääräykset.
Yritys oppi rakennusprojektista paljon – yksi selkeimmistä betonin 3D-tulostuksen hyödyistä on se, että materiaalia on mahdollista säästää huomattavia määriä, jopa 40% perinteiseen rakentamiseen verrattuna.
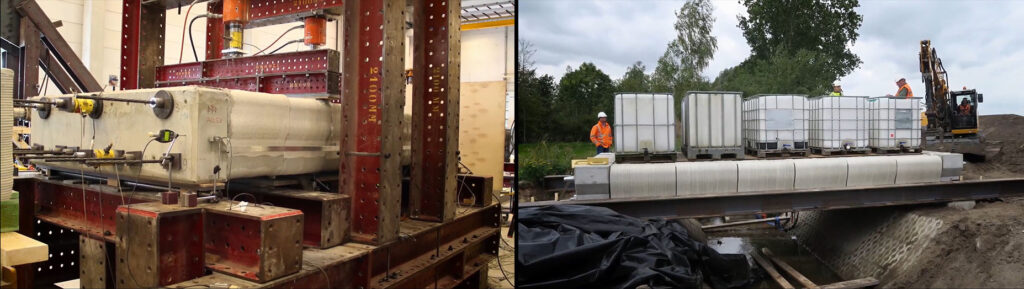
Science meets industry: Bruil prefab printing
Bruil on keskikokoinen rakennusalan yritys hollannissa, joka toimii 13 eri paikkakunnalla. Yrityksellä on 4 elementtitehdasta ja 2 kuivabetonitehdasta ja se toimittaa betonilaastia, kuivabetonia ja betonielementtejä rakennusalan tarpeisiin.
Yritys lähti mukaan “digitaaliseen betoniin” vuonna 2014, kun hollannissa oli lama, joka pakotti perinteisiä betonielementtejä- ja valuja tekevän yrityksen etsimään uusia toimintamalleja. Tästä johtuen yritys lähti vuonna 2015 kehittämään omaa betonin 3D-tulostuksen kokonaisratkaisua joka pitää sisällään ohjelmiston, tulostuslaitteiston ja materiaalin. Ohjelmistoratkaisussa robottien liikeradat/tulostuspolut muodostetaan Rhinon ja Grasshopperin yhdistelmällä. Yrityksellä on menossa useita betonin 3D-tulostusprojekteja, joista tässä esitellään kaksi eniten julkisuutta saanutta.
Bruilin tehtaalla on käytössä tulostuslaitteiston uusin versio, jossa robottina on KUKA K120 R3900 K-ultra KRC4 kontrollerilla ja 34 metrin lineaariradalla. Pitkä rata mahdollistaa kahden erillisen tulostusalueen hyödyntämisen. Tämä on tarpeen, sillä käytetyllä betonilla voi olla pitkäkin kovettumisaika. Tuotantolinjalla onnistuu myös valmistettujen elementtien pinnoitus. Valmistuksen jälkeen tuotantolinjalla 3D-skannataan valmistetut elementit, jotta varmistutaan siitä että ne ovat mittatarkkoja.
Esitys löytyy neljännen päivän Digital Concrete 2020 –videotiivistelmästä, mutta yritys on lisännyt suoran linkin myös youtube kanavalleen osoitteessa: https://www.youtube.com/watch?v=2j2RXRLsL7Y
Waterstoptaxi
Visuaalisesti näyttävä taksipysäkki “Waterstoptaxi” perustuu kuuteen kaksoiskaarevaan erilliseen elementiin, jotka liitetään toisiinsa esijännitettyjen teräskaapelien avulla. Esijännitettyjen kaapelien liittäminen kaareviin elementteihin on luonnollisesti haastavaa. Kaapelit kulkevat elementtien sisällä perustuksista päätyihin, ja ne keskitetään elementtien sisällä metallilevyjen avulla. Jotta bussipysäkki sai viranomaishyväksynnän, täytyi se suunnitella “design-by-testing” periaatteella, eli se rakennettiin täysikokoisena, jonka jälkeen sille tehtiin kuormitustestit heikkojen kohtien löytämiseksi. Testien jälkeen rakenne sai viranomaishyväksynnän, ja lopullinen versio on nyt rakenteilla. Yritys painotti hyvän viranomaisyhteistyön merkitystä, kun otetaan käyttöön uusia valmistusmenetelmiä. Taksipysäkki rakennetaan Rotterdamiin.
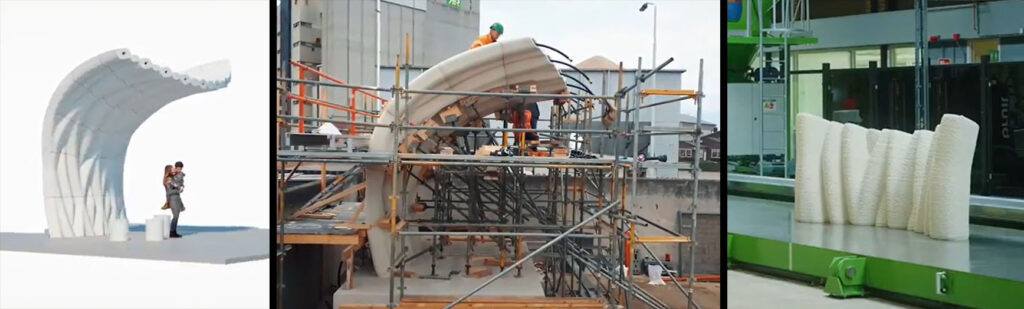
“Den Helder”
Yrityksen tämän hetken ykkösprojekti 3D-tulostukseen liittyen on ihan kohtalaisen kokoinen urakka ja yritys kutsuukin sitä yhdeksi maailman suurimmista betonin 3D-tulostusprojekteista. Kyseessä on kahden 1970 luvulla rakennetun asuinkerrostalon julkisivun ja parvekkeiden uudistaminen pohjois-hollannissa. Kerrostalossa on 154 asuntoa ja projektissa käytetään 125 erilaista 3D-tulostettua moduulia, joita on yhteensä 1200 kpl. 3D-tulostetut moduulit eivät ole kantavia rakenteita, vaan vanhan ulkoseinän ja uuden julkisivun väliin rakennettiin erillinen kantava rakenne, johon moduulit kiinnitetään. Tämä mahdollisti mm. yhden asiakkaan vaatimuksista joka oli suurempien parvekkeiden rakentamisen asuntoihin.
Projekti alkoi koko rakennuksen 3D-skannauksella, ja uuden rakenteen suunnittelu pohjautui skannattuun pistepilvimalliin. 3D-tulostuksen käyttäminen mahdollisti projektissa erilaisten moduulien käyttämisen ilman ylimääräistä vaivaa. Eri asuntojen välille tarvittavat muutokset olivat pieniä, mutta ne oli helppo ottaa huomioon suunnittelussa. Projektissa päädyttiin käyttämään 3D-tulostusta sen kustannustehokkuuden ja ympäristöystävällisyyden vuoksi. 3D-tulostusta hyödynnetään yleensä uusien kohteiden valmistuksessa, mutta tämä projekti osoittaa se soveltuu hyvin myös olemassa olevien rakennusten kunnostukseen ja päivittämiseen.
Projektista löytyy yrityksen yhteistyökumppanin sivuilta hieman lisätietoja: https://www.raptech.io/showcase-bruil
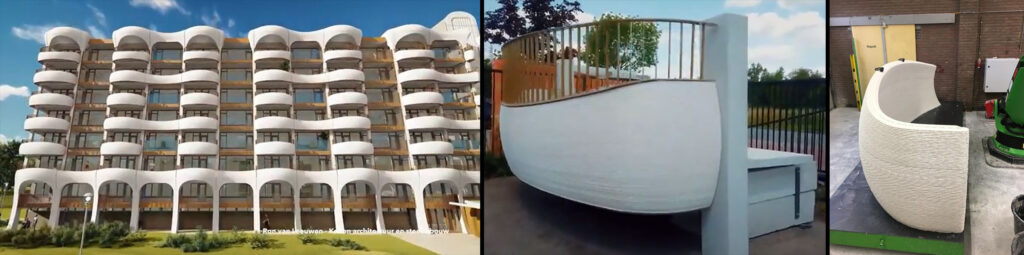
Savonialle hankitaan osana 3D-tulostuksen investointi- ja kehityshanketta betonin 3D-tulostuspää, jonka toimittaa suomalainen Hyperion Robotics (https://www.hyperionrobotics.com/). Toimitusaika on näillä näkymin marraskuun puoleen väliin mennessä. Mikäli aiheeseen liittyvä kehitystyö kiinnostaa, kannattaa olla yhteyksissä!
Antti Alonen
TKI-asiantuntija
Savonia-ammattikorkeakoulu

One thought on “Digital Concrete 2020 ja betonin 3D-tulostus (2/2)”
Comments are closed.