Pursottavissa ja jauhepetimenetelmään perustuvissa 3D-tulostimissa voidaan käyttää perinteisten muovien lisäksi komposiittimateriaaleja, eli muovin sekä kuitujen tai jauheen yhdistelmää. Markkinoilla onkin saatavilla muovimateriaaleja, joihin on yhdistetty esimerkiksi metallihiukkasia tai puu-, hiili-, kevlar- tai lasikuituja. Ekologisesta näkökulmasta biokomposiitit eli biopohjaisia kuituja hyödyntävät komposiittimateriaalit ovat tärkeä tutkimuksen ala. Kun muovimatriisina vielä käytetään biopohjaista PLA-muovia, on lopullinen tuote varsin ympäristöystävällinen verrattuna moniin muihin lämpömuovattaviin muoveihin.
Puukuitujen hyödyntäminen on mielekästä myös taloudellisesti, sillä puuteollisuuden ”nollakuidut” voidaan hyödyntää uudella tavalla, kun siitä tuotetaan raaka-ainetta 3D-tulostukseen. Kuitujen lisäys osaksi 3D-tulostusmateriaaleja vaikuttaa kuitenkin merkittävästi materiaalin ominaisuuksiin, sillä toistaiseksi biokomposiittien mekaaniset ominaisuudet jäävät perinteisten muovilaatujen jalkoihin. On kuitenkin huomioitava, että biokomposiittien kilpailuedut löytyvät muista ominaisuuksista. Ne ovat sekä edullisia että keveitä, ja puukuidun lisäys muovimatriisiin antaa sille todellisen puun tuntua ja visuaalisuutta, jolloin niitä voidaan käyttää sekä muovi- että puumateriaaleja korvaavina tuotteina sellaisissa kohteissa, joissa materiaalin mekaaniset ominaisuudet eivät ole ratkaiseva tekijä. Tässä kirjoituksessa perehdymme UPM Formi-biokomposiittien ominaisuuksiin sekä käsittelyyn.
Kuitumateriaalien 3D-tulostamiseen on olemassa myös ”continuous fiber”-3D-tulostusmenetelmä, jossa tulostuksen aikana kappaleeseen syötetään yhtenäistä kuitumateriaalia jatkuvana syöttönä. Tavallisissa komposiittiseoksissa <0,25 mm kokoluokan kuidut ovat jakautuneena tasaisesti materiaaliin, sillä liian suurilla kuiduilla ja partikkeleilla on taipumus aiheuttaa tukoksia suutinpäässä. Jatkuvatoimisella teknisen kuidun lisäysmenetelmällä tuotetut kappaleet ovat erittäin kestäviä; muoviset kappaleet voivat vastata mekaanisilta ominaisuuksiltaan jopa keveitä metalleja. Samaa ei voi sanoa perinteisistä kuitukomposiiteista, sillä kuidut voivat vaikuttaa heikentävästi mm. kerrosten kiinnittymiseen toisiinsa. Jatkuvatoiminen kuidun lisäys tulostuksen aikana vaatii kuitenkin 3D-tulostimen, joka on räätälöity tälle menetelmälle. Kuitukomposiittimateriaaleja puolestaan voivat tulostaa kaikki jauhepeti- ja materiaalia pursottavat tulostimet.
UPM Formi-granulaatti on UPM Biocomposites–yhtiön valmistamaa selluloosa-muovikomposiittimateriaalia, joka on tarkoitettu valu- ja ekstruusiotuotantoon. Valmiissa granulaatissa on 20 % tai 40 % selluloosaa, (tästä eteenpäin materiaaleihin viitataan nimillä UPM 20 ja UPM 40), lopun aineesta ollessa väritöntä PLA-muovia (kuvassa 1 vasemmalla). Näin ollen komposiittimateriaali on perinteisiä muoveja ekologisempaa, ja se voidaan sekä kierrättää että polttaa energiaksi jätteenpolttolaitoksessa. Tuoreen materiaalin väri on lähellä beigeä. Materiaalille on ominaista se, että sitä voi tummentaa mm. nostamalla prosessoinnin tai 3D-tulostuksen aikaista lämpötilaa tai jälkikäsittelemällä kappale 3D-tulostuksen jälkeen. 3D-filamentti voidaan myös värjätä lisäämällä granulaatin sekaan värillistä PLA-muovia tai muita värjääviä aineita filamentin valmistusvaiheessa. tarkempia tietoja tuotteesta on löydettävissä osoitteesta https://www.upmformi.com/.
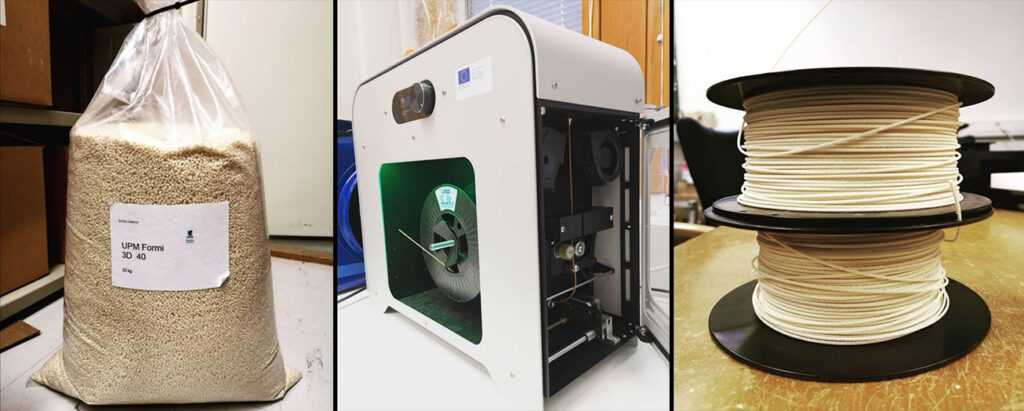
UPM Formi-filamenttien valmistus ja värjäys
UPM:n valmistamia biokomposiitteja on saatavilla sekä valmiina filamenttinä että granulaattimuotoisena. Granulaattimuotoista materiaalia käytetään yleensä suuremman mittaluokan 3D-tulostinten tai robotisoitujen 3D-tulostuspäiden kanssa kun materiaalien syöttönopeus on suuri. Yleistason “pöytäkokoluokan” laitteissa puolestaan käytetään filamentteja, jolloin vaihtoehtona on joko materiaalin ostaminen filamenttina (jos sitä on saatavilla) tai granulaatin muuttaminen filamentiksi.
Materiaalia ei ole saatavilla värjättynä, jolloin värimaailman laajentaminen vaatii myös toimenpiteitä tuotteen käyttäjältä. Tässä osiossa perehdytään UPM Formi-granulaateista valmistettujen filamenttien valmistamiseen sekä värjäämiseen.
Tutkimuksessa käytettiin UPM 20 ja UPM 40 granulaatteja. Filamentit tuotettiin 3DEVO Composer 450 Filament Maker-laitteella. Lämpötila-asetukset neljälle lämpötilavyöhykkeelle olivat 190/195/185/180 °C, ja ruuvin nopeudeksi säädettiin 5 kierrosta minuutissa. Filamentin värjäystä testattiin yksinkertaisesti UPM 40 granulaatilla ja PLA-tulostusjätteellä. Tulostuslaboratorioon kerääntynyttä harmaata tulostusjätettä rouhittiin SHR3D IT-silppurilla (valmistaja: 3devo), ja silppua lisättiin granulaatin sekaan noin 50–50 % massasuhteessa. Seos syötettiin filamentinvalmistuslaitteeseen, jossa käytettiin aiemmin mainittuja lämpötila- ja nopeussäätöjä.
Filamentin valmistaminen UPM:n granulaateista alkoi haasteilla. Biokomposiitit osoittautuivat materiaaleiksi, jotka eivät kuumennettuna siedä vetoa juuri lainkaan. Filamentinvalmistuslaitteessa olevan suutinpään halkaisija on tehdasasenteisena 4,00 mm, mikä mahdollistaa sekä 2,85 mm, että 1,75 mm standardifilamenttien valmistamisen. Koska testeissä käytettäviin 3D-tulostimiin sopii vain 1,75 mm filamentti, on materiaalia vedettävä suhteellisen rajusti, jotta oikea paksuus voidaan saavuttaa. Ero 4,00 mm alkupaksuuden ja 1,75 mm tavoitepaksuuden välillä oli liian suuri, eikä filamentti pysynyt ehjänä sitä vedettäessä. Siinä missä laitteesta saapuva perinteinen muovi venyy sitä vedettäessä, komposiittimateriaalilla on taipumus revetä. Tämä johtuu siitä, ettei kuitujen ja muovimatriisin välille synny kokonaisuutta koossa pitäviä vuorovaikutuksia. Tätä ongelmaa ei kyetty ratkaisemaan mm. pursotus- ja vetonopeutta säätämällä. Tilanne ratkaistiin koneistamalla laitteeseen uusi 2,00 mm halkaisijan pursotuspää.
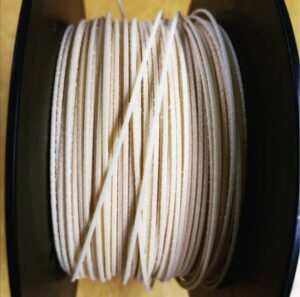
Filamentin tuottaminen onnistui pursotuspään vaihdon jälkeen pääasiassa hyvin. UPM 20 muuntui filamentiksi ilman suurempia ongelmia. UPM 40 % oli yksin liian kuitupitoista filamentin tuotantoa varten, joka näkyi repeilynä ja hilseilynä sitä vedettäessä sekä filamentin katkeamisherkkyytenä sitä käsiteltäessä. Testin aikana ei onnistuttu valmistamaan suurta määrää tulostettavaa UPM 40 filamenttia, edes parametreja säätämällä. Filamentin laatuun vaikuttava lämpötila haluttiin pitää filamentin valmistuksessa mahdollisimman alhaisena materiaalin lämpöhajoamisen minimoimiseksi. Liian alhainen lämpötila johti kuitenkin herkästi filamentin hilseilyyn (kuva 2) ja pinnan rosoisuuteen, kaupallisen puukuitufilamentin ollessa pinnaltaan huomattavasti sileämpää.
Testattujen filamenttipätkien pinnan epätasaisuudella ei kuitenkaan havaittu vaikutusta 3D-tulostettavuuteen tai tulostettujen kappaleiden laatuun, jolloin haitta jäi kosmeettiseksi. UPM 40-granulaatista saatiin valmistettua hyvin toimivaa materiaalia, kun sitä sekoitettiin puhtaan PLA-muovin kanssa 50–50 % massasuhteessa.
Värjätyn filamentin valmistaminen onnistui pääasiassa ongelmitta. Pursotusprosessissa tapahtui hetkittäisiä UPM 40 granulaatin työstöä muistuttavia häiriöitä, jotka saattoivat johtaa prosessin keskeyttämiseen. Laadultaan tuotettu filamentti vaikutti hyvältä, eikä se ollut UPM 40 tavoin erityisen haurasta (kuva 3a). Samoin filamentin 3D-tulostaminen onnistui ongelmitta ja filamentin kiinnittyminen tulostusalustaan oli erittäin tehokasta, tulostettuja kappaleita oli jopa haastava irrottaa alustastaan. Lisäksi tulostettaessa huomattiin, ettei filamentti ollut täysin tasalaatuista. Filamentin väri vaihteli hieman, toisinaan väri on puhtaan harmaa, ajoittain väri puolestaan muistutti enemmän puhdasta granulaattia. Tulostuksen laatuun värin vaihtelu ei kuitenkaan vaikuttanut.
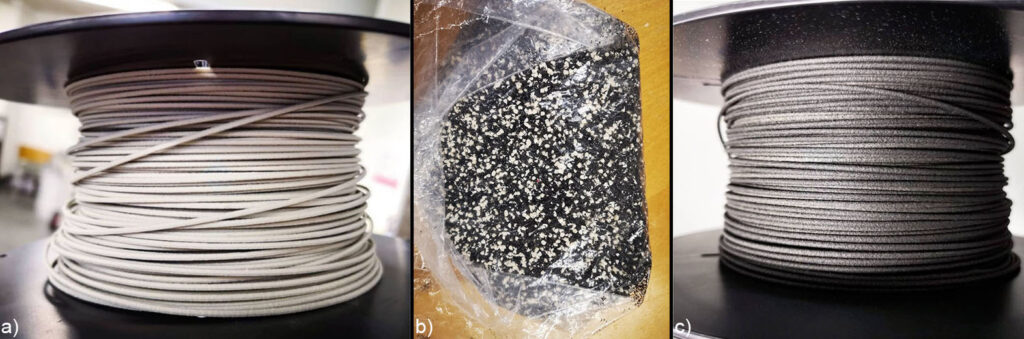
Filamentin homogenisointia testattiin uudestaan mustan PLA-jätemuovin avulla. Periaate oli sama, kuin aiemmin, mutta tällä kertaa PLA-rouhe sekä UPM 40-granulaatti rouhittiin yhteen sekoitettuna kertaalleen 3devo shr3dit -silppurilla. Tällöin granulaatinkin raekoko pieneni, eikä filamentin laadussa enää havaittu laatueroja sitä valmistettaessa (kuva 3b). Tuotettu filamentti oli laadultaan ja tulostettavuudeltaan erittäin hyvää ja tasaista (kuva 3c).
Vetolujuuskokeet
Minkä tahansa kuitujen tai partikkelien lisäys muovimatriisiin muuttaa alkuperäisen materiaalin lujuusominaisuuksia. Integroitavan materiaalin ominaisuudet, sekoitussuhteet sekä hyvin monet muut tekijät vaikuttavat lopputuotteen 3D-tulostettavuuteen sekä mekaanisiin ominaisuuksiin. Myös 3D-tulostusparametrit vaikuttavat lopullisen kappaleen ominaisuuksiin. Biopohjaisten kuitujen on havaittu vähentävän muovimateriaalin vahvuutta, mutta lisäävän sen jäykkyyttä – eli materiaalin kyky vastustaa olomuodon muutoksia lisääntyy, mutta kappale katkeaa helpommin. Uusien 3D-tulostusmateriaalien olisi yllettävä vähintään lähes yhtä hyviin ominaisuuksiin, kuin mihin kuluttajat ovat tottuneet, jotta tuote voi menestyä. Myös muilla hyvillä ominaisuuksilla, kuten ekologisuudella, on painoarvoa, mutta kuluttaja äänestää lompakollaan helposti parasta laatua – ja täten biokomposiittienkin täytyy kehittyä mekaanisilta ominaisuuksiltaan riittävän hyviksi, jotta niiden käyttö on mielekästä. Tässä osuudessa perehdytään biokomposiittien mekaanisiin ominaisuuksiin ja siihen, kuinka ne pärjäävät puhdasta muovia vastaan.
Seuraavista materiaaleista 3D-tulostettiin vetolujuussauvoja, joiden mekaaniset ominaisuudet määritettiin ASTM D638-standardin mukaisesti:
- UPM Formi 20 % granulaatista valmistettu biokomposiitti
- UPM Formi 40 % ja 3devo PLA granulaateista valmistettu biokomposiitti (50–50 % tilavuussuhde)
- Octofiber biokomposiitti (puukuitupitoisuus 20 %)
- FormFutura EasyWood biokomposiitti (puukuitupitoisuus 40 %)
- FormFutura Grey PLA
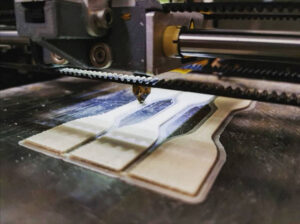
Tulostimena käytettiin ZMorph 2.0 SX-3D-tulostinta (kuva 4). Tulostuslämpötila oli 200 °C kaikilla filamenteilla, paitsi Octofiberin tapauksessa, tulostuspedin lämpötilan ollessa 60 °C. Octofiber ohjeistaa käyttämään hieman korkeampaa, 210–225 °C tulostuslämpötilaa, joten kyseinen filamentti tulostettiin 220 °C suuttimella. Kappaleet tulostettiin 100 % täytöllä ja materiaalinsyötöllä, sekä 0,2 mm kerroskorkeudella, jotka ovat eräitä tulostusprosessin sekä kappaleiden laatuun vaikuttavista parametreistä.
Puukuitufilamenttien kiinnittyminen puhtaaseen tulostusalustaan oli hieman haastavaa, sillä toisinaan materiaali irtosi tulostusalustasta välittömästi pursotuksen jälkeen. Alustan käsittely vedellä laimennetulla Eri Keeper-liimalla korjasi tilanteen, eikä irtoamista enää tapahtunut. Puhtailla PLA-filamenteilla tätä haastetta ei havaittu.
Biokomposiittimateriaalien hygroskooppisuus, eli taipumus sitoa ilmankosteutta itseensä (ominaista monille muillekin muovilaaduille) näkyi selvästi kaikissa, paitsi itse tuotetuissa tulostusmateriaaleissa, johtuen aiemmin mainittujen materiaalien pitkästä säilytysajasta. 3D-tulostuksen aikana tämä ilmeni vesihöyryn purkautumisena tulostuspäästä tulostuksen edetessä. Vesihöyryn purkautuminen voi osaltaan vaikuttaa tulostuksen laatuun ja sitä myötä tämän tutkimuksen tuloksiin. Myös PLA itsessään on hygroskooppista ainetta, mutta käytetty materiaali ei ollut ehtinyt sitomaan kosteutta.
Materiaalien ominaisuusmittaukset suoritettiin Itä-Suomen yliopiston Sovelletun fysiikan laitoksen Instron 8874-laitteella (Instron Corp.) tavallisissa huoneolosuhteissa. Mittaukset suoritti Itä-Suomen yliopiston sovelletun fysiikan maisteriopiskelija Isa Lyijynen.
Tuloksia
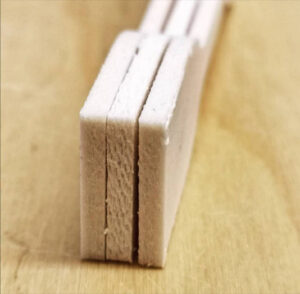
Biokomposiittien pinnanlaatu 3D-tulostettaessa oli pääosin hyvä. Kappaleissa ei havaittu dimensionaalisia poikkeamia, mutta tulostusjälki oli ajoittain aavistuksen onttoa (kuva 5). Tämä on tunnistettu ongelma biokomposiittien tulostuksessa, joka voidaan korjata lisäämällä materiaalinsyöttöä. Itsetehdyn filamentin tulostusjälki oli – jopa alkuperäisten odotusten vastaisesti – hieman kaupallista filamenttia parempi. Kappaleista tuli pinnaltaan tasaisempia, eikä mm. kappaleiden päihin muodostunut yhtä havaittavaa onttoisuutta, mitä kaupallisesta filamentista valmistetuissa kappaleissa voitiin nähdä. Tämä tosin johtuu todennäköisesti aiemmin mainitusta materiaalin hygroskooppisuudesta ja vesihöyryn purkautumisesta kaupallisia, huoneolosuhteissa säilytettyjä materiaaleja tulostettaessa.
UPM ilmoittaa UPM 20-tuotteelle vetolujuudeksi 28 MPa ja UPM 40-tuotteelle 48 MPa. Elastisuusmoduulien arvoiksi on vastaavasti ilmoitettu 2,6 GPa ja 5,4 GPa. Nämä tulokset ovat mitattu muottivaletuista kappaleista. 3D-tulostetuista kappaleista mitattuina mekaaniset ominaisuudet jäivät kauas ilmoitetuista arvoista (kuvat 6a ja 6b, esitetty keskiarvo ja vaihteluväli).
Myös muiden testattujen biokomposiittimateriaalien mekaaninen suorituskyky oli hyvin heikko verrattuna puhtaaseen PLA-muoviin. Tämä johtuu hyvin todennäköisesti 3D-tulostuksen ja muottivalun eroista, jotka heijastuvat kappaleen tiheyteen, täyttöasteeseen sekä sisäisiin liitoksiin. Muottivalettu kappale on varmasti täyttä tavaraa, eikä sen sisälle jää huomattavia ilmataskuja. 3D-tulostettujen kappaleiden sisälle todennäköisesti jää ilmaa, joka heijastuu suoraan kappaleen tiheyteen ja massaan. Materiaalin massan ja tiheyden on havaittu olevan yksi tärkeimmistä mekaanisia ominaisuuksia määrittävistä tekijöistä.
Toinen vaikuttava tekijä ovat materiaalin sisäiset liitokset. 3D-tulostetussa kappaleessa on kerroksia, joiden liittyminen toisiinsa voi olla heikkoa, varsinkin kun tilannetta verrataan muottivalettuun kappaleeseen, jossa kappale muodostuu käytännöstä yhdestä kerroksesta, jolloin mekaanisia ominaisuuksia heikentäviä liitoskohtia ei esiinny. Tässä kokeessa ei kuitenkaan testattu erilaisten 3D-tulostusparametrien vaikutusta mekaanisiin ominaisuuksiin, joten on hyvin mahdollista, että parempiin tuloksiin olisi voitu päästä mekaanisten ominaisuuksien osalta. Kaikki kappaleet 3D-tulostettiin samoja parametrejä käyttämällä. 3D-tulostettu PLA Grey oli mekaanisilta ominaisuuksiltaan kutakuinkin odotettujen arvojen tasolla, joten 3D-tulostuksen laatu oli oletettavasti hyvä ja parametrit säädetty tyydyttävästi ainakin tavallisimpien 3D-tulostusmuovien kannalta.

Kuitujen lisääminen muovimatriisiin lisää materiaalin elastisuusmoduulia eli lujuutta huomattavasti. Tämä voidaan huomata etenkin muottivaletuissa kappaleissa, mutta ero oli jopa päinvastainen 3D-tulostetuissa kappaleissa. Kirjallisuudessa tunnetaan ilmiö, jossa komposiittimateriaalin kuidut orientoituvat tulostuspään ja –suunnan mukaan ja kappale saa lisäkestävyyttä kuitujen säännöllisestä suuntautumisesta, mutta tällaista mekaanisia ominaisuuksia voimistavaa vaikutusta ei tässä testissä havaittu. Valetuissa kappaleissa kuidut järjestäytyvät satunnaisesti, eikä samankaltaista kestävyyttä lisäävää ilmiötä tapahdu. On kuitenkin mainittava, että testissä käytetyt biokomposiittimateriaalit eivät olleet laadultaan huippuluokkaa, sillä kaupallisia filamentteja oli säilytetty huoneolosuhteissa lukuisia kuukausia, sekä itse tuotetuissa UPM Formi-filamenteissa oli todennäköisesti laadullista vaihtelevuutta. Myöskään 3D-tulostusparametrit eivät olleet räätälöity biokomposiitteja varten, jolloin tulostuslaatuun jäi parantamisen varaa.
Tutkimuksen tässä vaiheessa voidaan todeta, että UPM Formin kaltainen väritön, värjättävä ja 3D-tulostettava biokomposiittimateriaali on hyvä tuote sen monipuolisuutensa ja ekologisuutensa vuoksi. Materiaalin muovaus ja värjäys omien tarpeiden mukaan onnistui helposti työhön sopivilla välineillä, ja lopputuotteeksi saatiin erinomaisesti toimivaa filamenttia itselle sopivassa värissä. Tuotteen huonot ominaisuudet liittyivät lähinnä filamentin hauraaseen rakenteeseen, jolloin materiaalilla oli perinteisiä filamentteja jokseenkin suurempi taipumus katketa. 3D-tulostettaessa tämä ei kuitenkaan ollut ongelma. Edellytykset biokomposiittien yleistymiselle kuluttajamarkkinoilla ovat olemassa.
Useat pursottamalla 3D-tulostetut kappaleet eivät välttämättä vaadi erityisen hyviä mekaanisia ominaisuuksia, jolloin tärkein kuluttajan tuotevalintaan aiheuttava tekijä on visuaalisuus. Näin ollen tarve öljypohjaisille muovimateriaaleille voi vähentyä ja alan ympäristöjalanjälki pienentyä yksinkertaisin toimenpitein. Biokomposiittimateriaalit voivat hyvinkin kattaa tulevaisuudessa merkittävän osan filamenttimarkkinoista, mikäli materiaalintuottajat ottavat ekologisuuden markkinaedukseen ja kehittävät kuluttajille vaihtelevia biokomposiittimateriaaleja. Tämä vaatii kuitenkin kehitystyötä myös puuteollisuuden toimijoiden kanssa, jotka tuottavat toimintansa sivutuotteena niin kutsuttua nollakuitua, joka voi jalostuksen kautta saada huomattavaa lisäarvoa – nykyään tuota kuitua hyödynnetään tuotteellisesti vain joissain määrin. Biokomposiittifilamenttien tulee kuitenkin olla riittävän tasalaatuisia ja 3D-tulostusystävällisiä, jotta ne voivat menestyä markkinoilla ja päihittää perinteiset filamenttimateriaalit. Kehitettävää ja mahdollisuuksia on, vaikkakin tässä tutkimuksessa tehdyt havainnot luovat biokomposiittimateriaaleista hieman heikon kuvan – mutta syyt niiden taustalla ovat tunnistettavia ja ratkaistavia.
Aiheeseen liittyviä kirjallisuuslähteita:
- A. Le Duigou, M. Castro, R. Bevan & N. Martin. 3D printing of wood fibre biocomposites: From mechanical to actuation functionality. Materials & Design 96:106-114 (2016).
- S. Wahab, A. Wagiman & M. Ibrahim. Development of wood-based composites material for 3D printing process. Applied Mechanics and Materials 315:987-991 (2013).
- M. Kariz, M. Sernek, M. Obućina & M. K. Kuzman. Effect of wood content in FDM filament on properties of 3D printed parts. Materials Today Communications 14:135-140 (2018).
- S. A. Raj, E. Muthukumaran & K. Jayakirshna. A Case Study of 3D Printed PLA and Its Mechanical Properties. Materials Today: Proceedings 5:11219-11226 (2018).
- B. M. Tymrak, M. Kreiger & J. M. Pearce. Mechanical properties of components fabricated with open-source 3-D printers under realistic environmental conditions. Materials & Design 58:242-246 (2014).
- N. G. Tanikella, B. Wittbrodt & J. M. Pearce. Tensile strength of commercial polymer materials for fused filament fabrication. Additive Manufacturing 15:40-47 (2017).
- A. Lanzotti, M. Grasso, G. Staiano & M. Martorelli. The impact of process parameters on mechanical properties of parts fabricated in PLA with an open-source 3-D printer. Rapid Prototyping Journal 21(5):604-617 (2015).
- J. Torres, J. Cotelo, J. Karl & A. P. Gordon. Mechanical Property Optimization of FDM PLA in Shear with Multiple Objectives. JOM: The Journal of Minerals, Metals & Materials Society 67(5):1183-1193 (2015).
- A. P. Mathew, K. Oksman & M. Sain. Mechanical properties of biodegradable composites from poly lactic acid (PLA) and microcrystalline cellulose (MCC). Journal of Applied Polymer Science 97(5):2014-2025 (2005).
Tämä kirjoitus liittyy Antti Väisäsen väitöskirjatutkimukseen jonka aiheena on 3D-tulostettavien muovimateriaalien työ- ja käyttöturvallisuus. Tutkimustyö toteutettiin yhteistyössä Savonian 3DTIK –hankkeen ja Itä-Suomen yliopiston kanssa. Aiemmin on tutkittu biokomposiittimateriaalien pienhiukkaspäästöjä, niihin liittyvä blogikirjoitus löytyy osoitteesta: https://blogi.savonia.fi/3dtulostus/2018/10/31/jatemuovista-ja-kotimaisesta-puusta-3d-tulostusmateriaaleiksi/
Antti Väisänen
projektityöntekijä, Savonia-ammattikorkeakoulu
apurahatutkija, Sisäympäristön ja työhygienian tutkimusryhmä, Ympäristö- ja biotieteiden laitos, Itä-Suomen yliopisto
Antti Alonen
tki-asiantuntija
Savonia-ammattikorkeakoulu

One thought on “UPM Formi: Biokomposiittigranulaatista 3D-tulostusfilamentiksi – värjäys ja mekaaninen suorituskyky”
Comments are closed.
Hei, Kiitos kattavasta tutkimuksesta! Olemme huomanneet paljon samoja asioita biokomposiittifilamenttien suhteen. 20% sellulloosakuitua ei toimi filamentissa ihan riittävän hyvin, siksi suosittelemme filamenttivalmistajille 25% 3D40 75% PLA suhdetta eli vain 10% kuitupitoisuutta. 3D40 on konsentraattilaatu ja ei siksi toimi sellaisenaan. Kaupallisesta puolelta kannattaa katsoa esim. AddNorthin Textura brändin alla olevat filamentit.